Introduction to Aluminum Manufacturing
Aluminum manufacturing stands at the forefront of modern industrial processes, showcasing a blend of complex chemical engineering and metallurgical techniques. This process begins with the extraction of alumina from bauxite ore, a procedure integral to aluminum production. Aluminum’s ubiquitous presence in industries ranging from construction and transportation to packaging and electronics underlines its significance. The journey of aluminum from its raw form as bauxite to the refined and versatile metal is a testament to the ingenuity and sophistication of modern manufacturing. This process not only encompasses the transformation of bauxite but also involves intricate procedures to enhance the metal’s properties, ensuring its suitability for a wide array of applications. The role of aluminum factories in this transformative process is critical, as they employ cutting-edge technology and innovative methods to meet the growing global demand for aluminum.
The Bayer Process: Extracting Alumina from Bauxite
The Bayer process, a pivotal step in aluminum manufacturing, involves the extraction of alumina from bauxite ore. This process begins with bauxite grinding, where the mineral is refined to produce a consistent material. The ground bauxite is then subjected to the Bayer process, which involves mixing it with a caustic soda solution under high pressure and temperature to produce sodium aluminate, also known as slurry. The byproduct of this reaction, red mud, contains impurities like iron, silicon, and titanium, and is carefully separated from the alumina. The solution undergoes settling and filtration to remove excess red mud and other solids. This method is fundamental in aluminum factories, as it efficiently extracts pure alumina, a white powder known as aluminum oxide, from bauxite. The Bayer process is a cornerstone of the aluminum industry, setting the stage for the subsequent transformation of alumina into aluminum.
From Alumina to Aluminum: The Hall-Héroult Process
The transformation of alumina into aluminum is achieved through the Hall-Héroult process, a smelting method that plays a central role in aluminum production. In this process, refined alumina is poured into a reduction cell containing molten cryolite at approximately 950°C. Here, a strong electrical current is passed through the mixture, breaking the bond between aluminum and oxygen. The result is 99.8% pure aluminum, a remarkable feat of chemical engineering. This process is integral to aluminum factories, embodying the advanced technological capabilities required to produce aluminum. The Hall-Héroult process not only signifies the final stage in the transformation of bauxite into aluminum but also highlights the intricate balance of temperature, pressure, and electrical current necessary to achieve this transformation. The efficiency and effectiveness of this process have made it the standard in aluminum manufacturing worldwide.
Aluminum Alloying and Forming Techniques
Once aluminum is extracted, it undergoes various alloying and forming techniques to enhance its properties for diverse applications. Alloying involves adding elements like magnesium silicide to pure aluminum to increase its strength and corrosion resistance, resulting in materials like the 6000 series alloys. Aluminum factories then employ different forming methods to shape the alloy. Extrusion is a widely used technique, where the aluminum alloy is heated and pushed through a die to create a fixed cross-sectional profile. Rolling involves casting the alloy into beams and rolling them into thin sheets, suitable for products like beverage cans. Foundry alloys, another method, involve cold-chamber casting where the aluminum is shaped into desired forms for applications in industries like aerospace and electronics. These techniques demonstrate the versatility and adaptability of aluminum, making it a preferred material in various sectors.
The Role of Recycling in Aluminum Production
Recycling plays a crucial role in the lifecycle of aluminum, significantly reducing the environmental impact of aluminum production. Aluminum factories prioritize recycling due to its efficiency, as it requires only 5% of the energy used in producing new aluminum. The process involves sorting, cleansing, and remelting scrap aluminum to form molten aluminum, which is then processed into ingots for further use. This cycle of recycling enables the aluminum industry to minimize waste and conserve natural resources. The fact that aluminum can be recycled repeatedly without losing its natural qualities makes it an environmentally friendly material. Aluminum factories are increasingly focusing on enhancing their recycling processes, reflecting a commitment to sustainability and responsible manufacturing practices.
Conclusion
In conclusion, the world of aluminum factories is a realm where advanced science and engineering converge to produce one of the most versatile and widely used metals. From the initial extraction of alumina to the final steps of alloying and recycling, the journey of aluminum is marked by a series of intricate and efficient processes. These factories not only cater to the ever-growing global demand for aluminum but also play a significant role in driving innovation and sustainability within the industry. As we move forward, the importance of aluminum factories in both the economic and environmental landscapes will undoubtedly continue to grow, making them pivotal players in the future of manufacturing.
Frequently Asked Questions
Q1: What is the Bayer Process in aluminum manufacturing?
A1: The Bayer Process is a method of extracting alumina from bauxite ore. It involves grinding bauxite and treating it with a caustic soda solution under high pressure and temperature to produce sodium aluminate. This process is vital for producing the alumina used in aluminum manufacturing.
Q2: How is aluminum extracted from alumina?
A2: Aluminum is extracted from alumina through the Hall-Héroult process. This involves pouring refined alumina into a reduction cell with molten cryolite and passing an electrical current through it, resulting in 99.8% pure aluminum.
Q3: What are the common methods for forming aluminum in factories?
A3: Common aluminum forming methods in factories include extrusion, rolling, and foundry alloys. Extrusion involves heating and pushing aluminum through a die, rolling flattens it into thin sheets, and foundry alloys involve shaping aluminum in molds for specific applications.
Q4: Why is recycling important in aluminum production?
A4: Recycling is crucial in aluminum production as it conserves energy and natural resources. It requires only 5% of the energy used to produce new aluminum and enables the material to be reused without losing its properties.
Q5: What future trends are expected in aluminum manufacturing?
A5: Future trends in aluminum manufacturing include technological advancements for greater efficiency, innovations for more sustainable practices, and enhanced recycling processes to reduce the environmental impact.
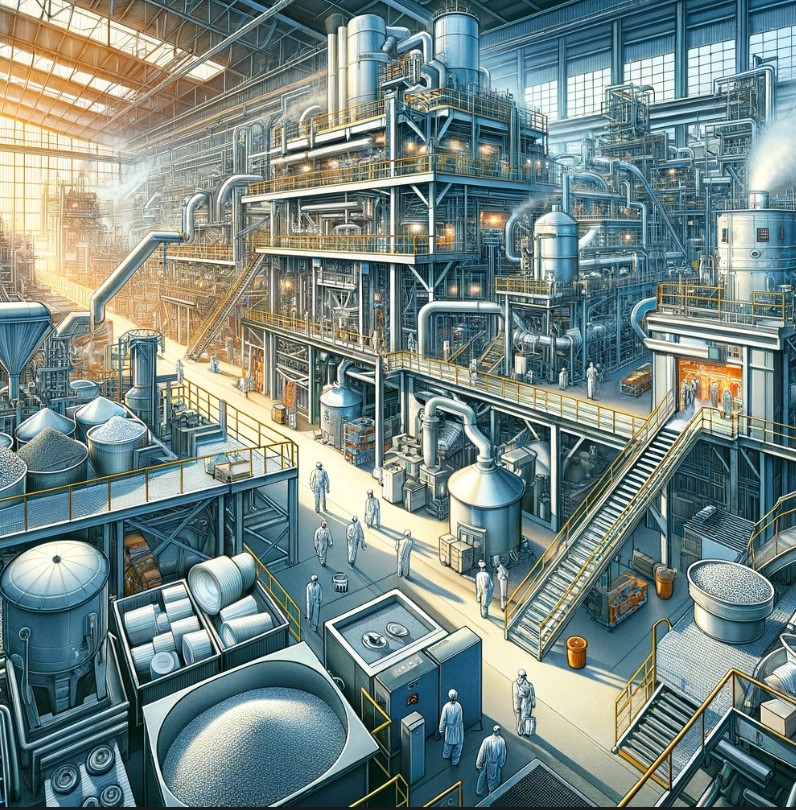