Introduction
In the realm of aluminum extrusion, the design of cross-sections plays a pivotal role in achieving efficiency and precision. This article delves into the intricacies of designing aluminum profile cross-sections, exploring key factors that influence the extrusion process.
Main Factors in Designing Aluminum Profile Cross-Sections
A. Cross-Sectional Size:
- The circumscribed circle as a measure of cross-sectional size and its impact on extrusion force requirements.
B. Complexity of Cross-Sectional Shape:
- Categorization of aluminum profiles into solid, semi-hollow, and hollow, based on their cross-sectional shapes.
C. Squeeze Coefficient:
- The significance of choosing a reasonable extrusion coefficient to facilitate deformation without hindering the extrusion process.
D. Aluminum Profile Wall Thickness:
- Determinants of wall thickness, including the circumscribed circle, alloy composition, and shape factors, affecting extrusion ease.
E. Design of Enclosed Space Area:
- Challenges posed by cantilever beams in thin and deep profiles, exploring the intricacies of the design.
F. Corner Radius Between Right Angles:
- Examination of corner radius importance, stress concentration, and wear issues related to right angles in aluminum profiles.
G. Section Size Tolerance of Aluminum Profiles:
- Consideration of cross-section size tolerance based on processing allowance, usage conditions, difficulty of extrusion, alloy grade, and shape location.
H. Other Design Elements:
- Recognition of diverse aluminum alloy profiles, emphasizing the consideration of special design elements.
Conclusion
Crafting aluminum profiles through extrusion is a nuanced process, and the design of cross-sections is a critical determinant of success. By understanding and carefully considering factors like size, shape, and tolerance, manufacturers can optimize efficiency and precision in the extrusion of aluminum profiles.
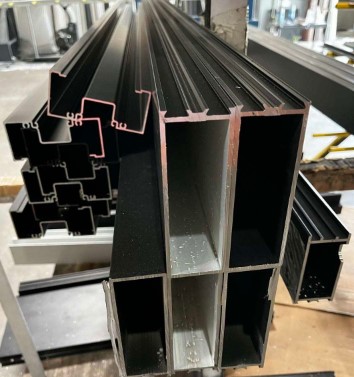