Decoding the Metals: A Comprehensive Comparison Between 7075 and 6061 Aluminum Alloys
Aluminum alloys stand at the forefront of modern engineering and design, offering a remarkable blend of strength, durability, and lightweight properties. Among the myriad of options, 7075 and 6061 aluminum alloys emerge as prominent choices, each with unique characteristics that cater to specific industrial needs. This article delves into the nuances of these two alloys, helping you decide which is best suited for your project.
Composition and Alloying Elements
The 7075 aluminum alloy, often referred to as the “super aluminum,” boasts a primary alloying element of zinc, constituting up to 6% of its composition. This high zinc content bestows the alloy with superior strength, pushing its capabilities to match, and at times surpass, those of steel. In contrast, the 6061 aluminum alloy leans on magnesium and silicon as its chief alloying elements, offering a more balanced strength-to-flexibility ratio, making it versatile for various applications.
Strength and Durability
When it comes to strength, 7075 undoubtedly takes the lead. Its robust nature makes it a go-to for applications where strength is non-negotiable, such as in aerospace and competitive sports equipment. However, 6061 is no slouch; its admirable strength coupled with enhanced corrosion resistance makes it ideal for architectural and automotive applications, where longevity and aesthetics are key.
Cost and Availability
The superior strength of 7075 comes with a higher price tag, making it a less economical choice for projects where budget constraints are a concern. On the other hand, 6061 aluminum alloy is renowned for its cost-effectiveness and widespread availability, making it a staple in the manufacturing world.
Practical Applications and Machinability
The practicality of 7075 and 6061 aluminum alloys extends into their applications and machinability. The 7075’s challenge in welding and processing confines its use to specific areas that can bypass these limitations. In contrast, 6061’s excellent machinability, including its ability to be easily welded and formed, makes it a versatile choice for a wide range of projects, from construction to custom fabrications.
Comparison with Zinc Alloy
Venturing beyond aluminum, zinc alloys present an alternative with distinct properties, notably in their lower melting point and versatile casting capabilities. However, when it comes to strength and thermal resistance, aluminum alloys, particularly 7075 and 6061, stand out, offering broader applications in more demanding environments.
Choosing the Right Alloy for Your Needs
Selecting between 7075 and 6061 aluminum alloys boils down to understanding your project’s specific requirements. For applications demanding utmost strength and durability, 7075 is the clear choice. Conversely, for projects requiring a balance between strength, flexibility, and cost, 6061 proves to be a versatile and practical option.
Conclusion
The decision between 7075 and 6061 aluminum alloys involves a careful consideration of their composition, strength, cost, and practical applications. By understanding the unique properties and benefits of each alloy, engineers and designers can make informed choices, ensuring the success of their projects. Whether you’re designing a high-performance sports equipment or an architectural masterpiece, the right aluminum alloy can make all the difference.
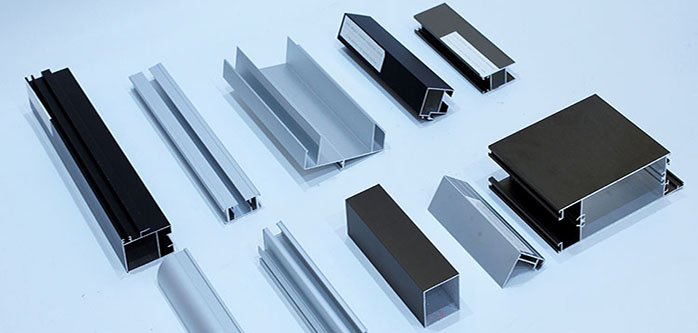