The 6063 aluminum profile stands as a testament to the ingenuity and precision inherent in modern manufacturing processes. Favored for its balance of strength, flexibility, and aesthetic appeal, the 6063 series finds itself at the heart of numerous projects across the industrial and construction sectors. Let’s explore the meticulous journey these profiles undergo from raw aluminum to finished product.
The Extrusion Process Explained
1. Selection of Raw Materials
The journey begins with the selection of high-quality 6063 aluminum ingots. The purity and composition of these ingots play a pivotal role in defining the mechanical properties of the final profiles, making this step crucial for ensuring top-notch product performance.
2. Aluminum Rod Heating
Precision in temperature control is vital during the heating of aluminum rods. The aim is to achieve a perfect balance that neither compromises the hardness of the extruded profiles nor their structural integrity, setting the stage for high-quality outcomes.
3. Mold Design and Maintenance
Extrusion molds are engineered with exceptional precision, designed to produce profiles that meet specific requirements. Regular maintenance ensures these molds continue to deliver profiles with the exact dimensions and quality needed, underscoring the importance of meticulous design and upkeep.
4. The Extrusion Process
This step is where the heated aluminum rods are transformed into profiles, pushed through molds under immense pressure. Key factors, including extrusion temperature and speed, play critical roles in ensuring the profiles’ mechanical properties and surface quality meet industry standards.
5. Straightening and Correction
Post-extrusion, profiles often require straightening to correct any deviations. This step ensures each profile adheres to strict tolerance ranges, a testament to the precision expected in final products.
6. Artificial Aging
To attain the desired hardness and strength, profiles undergo an artificial aging process. This step is crucial for transforming the extruded aluminum into a material capable of withstanding the demands of its application.
7. Surface Treatment
Surface treatments, such as sandblasting and oxidation, enhance the profiles’ aesthetic and functional qualities. These processes not only improve appearance but also contribute to the profiles’ durability and resistance to environmental factors.
8. Packaging
The culmination of the extrusion process is packaging, which is meticulously designed to protect the profiles’ surfaces. This final step ensures that the profiles arrive at their destination in pristine condition, ready for use in various applications.
Practical Applications and Considerations
6063 aluminum profiles are celebrated for their versatility, finding applications ranging from architectural frameworks to intricate industrial machinery. Understanding the nuances of their production process can aid professionals in selecting the ideal profile for their specific project needs, ensuring both functionality and form are seamlessly integrated.
Conclusion
The extrusion of 6063 aluminum profiles embodies the convergence of art and science in manufacturing. Each step, from raw material selection to final packaging, is executed with precision, underscoring the dedication to quality that defines the aluminum industry. For professionals navigating these choices, the insights into this process are invaluable, offering a foundation for informed decision-making that leverages the full potential of 6063 aluminum profiles in their projects.
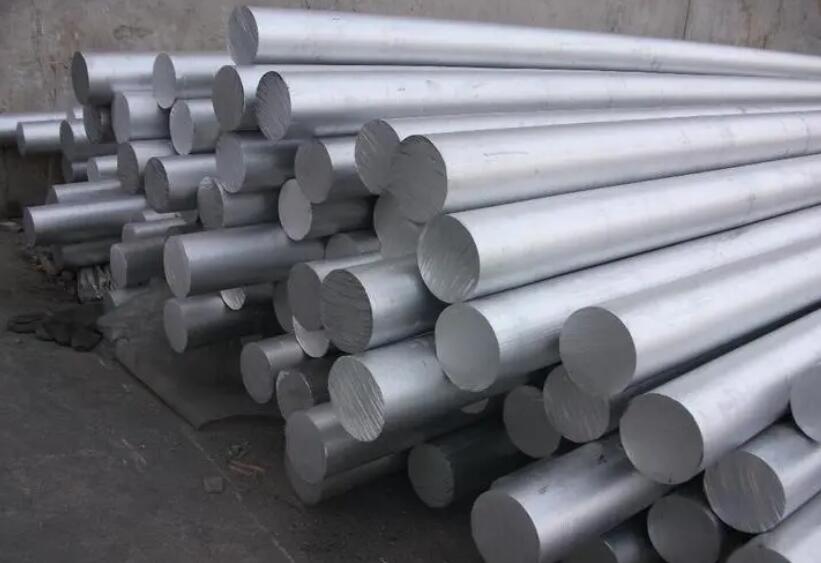