Introduction
Industrial aluminum profiles play a crucial role in various industries due to their versatility and durability. However, surface defects such as yellowing can occur during production, impacting both aesthetics and performance. Let’s delve into the causes of surface yellowing in industrial aluminum profiles and explore preventive measures to maintain their quality.
Causes of Surface Yellowing in Industrial Aluminum Profiles
A. Improper Coolant Usage during Extrusion: During the extrusion process, coolant is essential for cooling the profile and enhancing its properties. However, using water-based coolant or coolant with high copper content can lead to surface yellowing due to chemical reactions with the active aluminum metal.
B. Inadequate Surface Cleaning before Treatment: Effective surface treatment, such as oxidation, requires a clean profile surface free from oil stains. Incomplete cleaning can hinder the formation of an even oxide film, resulting in surface yellowing or inconsistent coloration.
Prevention and Solutions
A. Proper Selection and Usage of Coolant: Choose coolant types compatible with aluminum to avoid adverse reactions. Implement techniques to minimize surface reactions during the cooling process, ensuring optimal profile quality.
B. Thorough Surface Cleaning Procedures: Prioritize thorough cleaning of the profile surface to remove oil stains completely. A clean surface facilitates uniform oxide film formation, reducing the risk of surface defects like yellowing.
Conclusion
Surface yellowing in industrial aluminum profiles can be mitigated through proper coolant selection and surface cleaning procedures. By implementing preventive measures, manufacturers can maintain the quality and aesthetics of aluminum profiles, ensuring optimal performance in various applications.
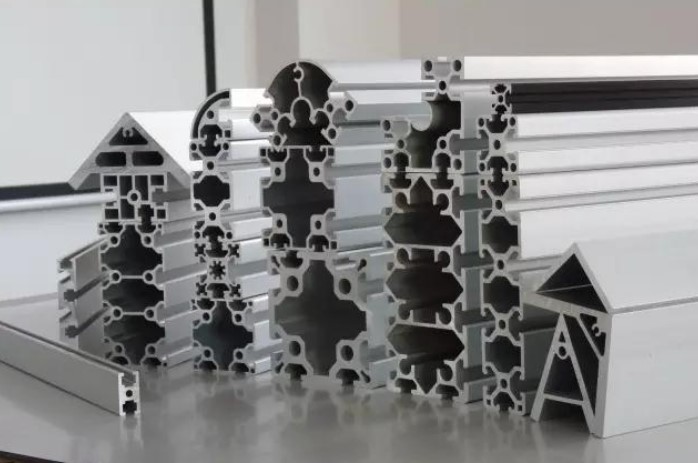