Introduction
In today’s manufacturing landscape, surface treatment plays a pivotal role in elevating product aesthetics and functionality. Among the myriad of surface treatment techniques, mirror polishing aluminum alloys stands out as a key process for enhancing the appearance and performance of aluminum alloy products.
Importance of Aluminum Alloy Surface Treatment
Aluminum alloys undergo various manufacturing processes that may introduce surface defects, oxide layers, or machining marks. Surface treatment becomes essential to address these imperfections, improving not only the product’s visual appeal but also its corrosion resistance and mechanical properties.
Aluminum Alloy Polishing Process
The mirror polishing process involves meticulous steps, from pretreatment to final processing, to achieve a flawless mirror-like surface finish. Each stage, including pretreatment, coarse grinding, polishing, and final processing, contributes to enhancing the brightness and smoothness of the aluminum alloy surface.
Applications of Polished Aluminum Alloys
Polished aluminum alloys find extensive applications across diverse industries. From automotive components to household items and aerospace structures to electronic products, the mirror-like brightness of polished aluminum alloys adds a touch of elegance and sophistication to various end products.
Precautions in Aluminum Alloy Polishing
While mirror polishing offers numerous benefits, it requires careful consideration and precise process control. Factors such as material selection, process control, and safety protection are paramount to ensure successful and safe production of polished aluminum alloys.
Conclusion
The mirror polishing process not only improves the appearance quality of aluminum alloy products but also broadens their application horizons. As surface treatment technology continues to evolve, the allure of mirror polishing aluminum alloys is expected to shine brightly across industries, meeting consumers’ demand for high-quality, aesthetically pleasing products.
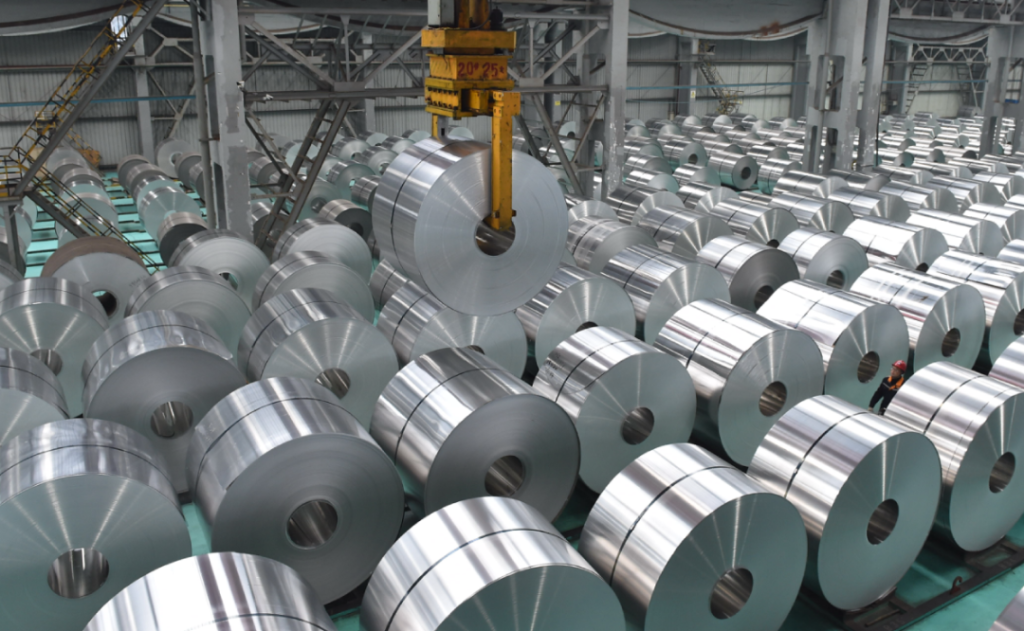