Introduction
Industrial aluminum profiles are a cornerstone in the realm of automation equipment, serving as essential accessories and supports. These profiles, prized for their beauty, ease of formation, and relative hardness, often require additional processing to maximize their utility. One such process is anodizing, which significantly enhances the properties of aluminum profiles. This article explores the various reasons why anodizing is crucial for industrial aluminum profiles and delves into its wide-ranging benefits.
Reasons for Anodizing Aluminum Profiles
Improve Corrosion Resistance
Aluminum is naturally corrosion-resistant due to the formation of a thin oxide film when it reacts with oxygen in the air. However, this natural oxide layer is often uneven and thin, making it susceptible to scratches and weaker in corrosion resistance. Anodizing addresses these issues by creating a uniform, dense oxide film that offers superior protection against corrosion. This enhanced layer ensures the longevity and durability of aluminum profiles, especially in environments where corrosion is a significant concern.
Enhance Wear Resistance
While aluminum alloys are known for their versatility, they are not as hard as steel, making them prone to scratches and wear. Anodizing significantly increases the surface hardness of aluminum profiles, with oxide film hardness reaching up to 300HV. This increased hardness translates into better wear resistance, making anodized aluminum profiles ideal for applications where durability is paramount.
Surface Coloring for Decorative Purposes
Before anodizing, aluminum profiles have many tiny pores on their surface. These pores can absorb dyes and metal salts, allowing for a variety of rich colors to be imparted to the aluminum products. This capability is particularly valuable for decorative applications, where aesthetic appeal is as important as functional performance. Anodizing thus opens up a myriad of possibilities for customizing the appearance of aluminum products to meet specific design requirements.
Improve Insulation
Aluminum’s excellent conductivity is beneficial in many applications, but there are situations where insulation is needed. The oxide film produced by anodizing is non-conductive, making anodized aluminum profiles suitable for use in electrical insulation. This property expands the usability of aluminum profiles in electronic and electrical applications where preventing conductivity is crucial.
Prepare Surface for Spray Painting
Anodized aluminum profiles have surface voids that exhibit strong adsorption properties, making them excellent candidates for spray painting. The enhanced adhesion provided by these voids ensures that the spray paint is applied more uniformly and adheres better, resulting in a smoother and more aesthetically pleasing finish. This is particularly important for applications requiring high-quality painted surfaces.
Additional Benefits and Future Applications
Beyond the immediate benefits, anodizing aluminum profiles holds promise for broader applications in science and technology. As the process continues to evolve, it is likely that anodized aluminum will find new uses across various fields, further cementing its role in modern industry.
Conclusion
Anodizing industrial aluminum profiles offers a multitude of benefits, from improved corrosion and wear resistance to enhanced aesthetic appeal and electrical insulation. These advantages make anodized aluminum profiles indispensable in many industrial applications, driving innovation and efficiency. As technology advances, the process of anodizing will undoubtedly continue to expand its reach, unlocking new potentials and applications for aluminum profiles in the future.
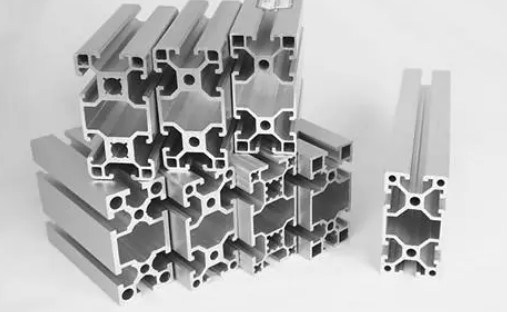