Introduction
In the construction industry, aluminum panels are highly valued for their versatility and functionality. Among the popular choices are honeycomb aluminum panels and aluminum veneer. Both materials offer unique benefits and have specific applications. In this article, we will explore the main advantages and disadvantages of these materials, helping you make an informed decision for your construction projects.
Section 1: Advantages of Honeycomb Aluminum Panels
Flat Surface and Uniform Color Honeycomb aluminum panels boast a flat surface with uniform color due to the roller coating process, which ensures high production efficiency, uniform coating, and good adhesion. The surface is treated with fluorocarbon resin, providing strong corrosion and scratch resistance.
Diverse Colors These panels come in a wide array of colors and coatings, including fluorocarbon spraying and wood grain transfer. This variety allows for extensive customization based on project needs.
Sound Insulation, Heat Insulation, Fire Prevention, and Heat Preservation The closed honeycombs within the panels block air circulation, providing excellent sound insulation. Additionally, aluminum’s non-combustible nature offers fire prevention benefits, while the structure helps in heat preservation.
Environmental Protection, Energy Saving, Easy Installation Honeycomb aluminum panels are eco-friendly, cost-effective, and durable. They are easy to install, making them a practical choice for many construction projects.
Section 2: Disadvantages of Honeycomb Aluminum Panels
High Production Cost The composite processing involved in manufacturing these panels increases production costs, making them more suitable for mid-to-high-end projects.
Limited Plasticity The plasticity of honeycomb aluminum panels is limited, restricting the variety of shapes and types that can be produced.
Section 3: Advantages of Aluminum Veneer
Low Cost Aluminum veneer production utilizes advanced coating technology with a high utilization rate of fluorocarbon paint, making it an energy-saving and environmentally friendly product.
High Strength Manufactured using high-grade aluminum alloy plates, aluminum veneer ensures excellent wind, earthquake, leakage, and impact resistance.
Flame Retardancy Made entirely of aluminum with a high-quality fluorocarbon coating, aluminum veneer is non-combustible, offering significant fire safety advantages.
Light Material Aluminum veneer is extremely lightweight, only a fraction of the weight of glass or stone curtain walls, making it easier to handle and install.
Good Processability Aluminum veneer can be easily bent, punched, and welded into various geometric shapes, meeting diverse architectural requirements.
Corrosion Resistance The high fluorocarbon resin content in the surface PVDF provides robust protection against acid rain, air pollutants, and UV rays, preventing discoloration and peeling.
No Light Pollution The matte finish of the fluorocarbon coating minimizes light pollution, a significant advantage over glass curtain walls.
Diverse Colors With over 100 available colors, aluminum veneer offers extensive customization, including imitation stone and wood grain effects.
Recyclability Aluminum veneer can be recycled and reused, making it an environmentally sustainable choice.
Section 4: Disadvantages of Aluminum Veneer
Anti-Deformation Requirements Each part of the curtain wall system must be carefully calculated to withstand deformation caused by wind pressure, weight, earthquakes, and temperature changes.
Potential for Inconsistent Force Distribution Inconsistent force at fixed points can cause surface deformation, affecting the appearance. Ensuring a uniform fixing method is crucial to maintaining the flatness of the curtain wall surface.
Section 5: Honeycomb Aluminum Panels vs. Aluminum Veneer: A Comparative Analysis
Production and Processing Aluminum veneer is simpler to produce and process, with various shapes achievable. Honeycomb aluminum panels, being composite, have a slower processing speed and lower capacity.
Structural Integrity Honeycomb panels do not require additional reinforcement due to the internal aluminum honeycomb core, unlike aluminum veneer, which needs ribs for larger dimensions, potentially causing unevenness due to different thermal expansion coefficients.
Material Properties Both materials are lightweight, strong, flat, easy to install and maintain, environmentally friendly, and resistant to thermal expansion and contraction. However, honeycomb panels offer higher compressive resistance and are better suited for large-size panels.
Durability and Limitations Aluminum veneer is generally more durable for building curtain walls, whereas honeycomb panels are limited by composite glue, which may affect long-term performance.
Section 6: Application Scenarios and Selection Criteria
Honeycomb Aluminum Panels Typically used in applications requiring superior sound insulation, fire resistance, and thermal preservation. Ideal for high-end projects where cost is less of a constraint.
Aluminum Veneer Preferred for applications needing diverse shapes, low cost, and high strength. Suitable for both budget-conscious projects and those requiring high aesthetic appeal.
When choosing between the two, consider the specific requirements of your project, including budget, desired properties, and long-term performance needs.
Conclusion
Honeycomb aluminum panels and aluminum veneer each have their distinct advantages and disadvantages. The best choice depends on the specific needs of your project. By understanding the properties and applications of these materials, you can make an informed decision that ensures optimal performance and aesthetic appeal for your construction projects.
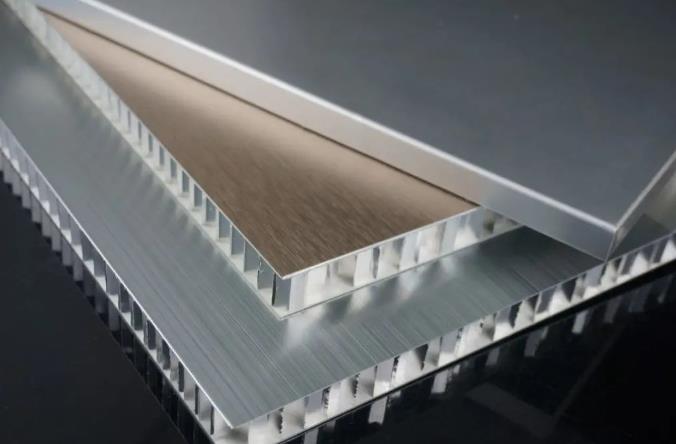