Introduction
Aluminum profiles play a crucial role in various industries, often requiring precise customization and complex assembly. CNC (Computer Numerical Control) machining has revolutionized the production of aluminum profiles, offering high precision and efficiency. This guide explores key CNC finishing processes essential for optimizing aluminum profile manufacturing.
Aluminum Profile Laser Cutting: Precision at Its Best
Laser cutting is integral to CNC processing, allowing aluminum profiles to be cut precisely according to design specifications. This method ensures accuracy and flexibility in producing profiles of varying lengths and configurations.
CNC Punching: Enhancing Connectivity
CNC punching is pivotal in aluminum profile assembly, facilitating the creation of holes and connections without the need for welding. From buried holes to step holes, each punch type serves specific structural and functional purposes.
Aluminum Profile Tapping: Strengthening Structural Integrity
Tapping external threads on aluminum profiles ensures secure fastening and structural integrity. This process, aligned with design drawings’ specifications, supports efficient assembly and enhances overall stability.
CNC Machining Center: Precision in Complexity
While basic assembly of aluminum profiles may not always require CNC machining centers, these advanced tools are indispensable for complex projects and non-standard parts. They enable intricate machining operations that traditional methods cannot match.
Conclusion
CNC finishing processes are indispensable in modern aluminum profile production, offering unparalleled precision, cost-effectiveness, and versatility. As industries evolve, leveraging CNC technology will continue to drive innovation and efficiency in aluminum profile manufacturing.
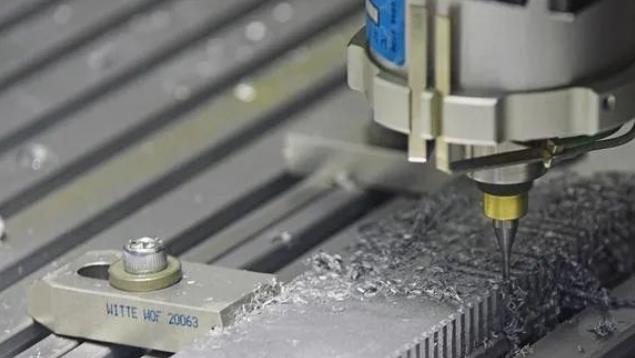