Aluminum alloy products undergo a meticulous preparation process before anodizing to ensure optimal surface quality and finish durability. Among these preparatory steps, sandblasting stands out as a crucial procedure that significantly enhances the outcome of the anodizing process.
Introduction
In industries ranging from architecture to electronics, aluminum alloys are valued for their lightweight properties and structural integrity. Before these alloys undergo anodizing—a process that enhances corrosion resistance and aesthetic appeal—they must first undergo thorough surface preparation, with sandblasting playing a pivotal role.
Basic Principle of Sandblasting
Sandblasting involves the use of high-speed sand particles to impact the surface of aluminum alloy products, effectively removing surface oxide layers, oil residues, dust particles, and micro burrs. This process is preceded by degreasing and water washing to eliminate any remaining contaminants, ensuring a pristine surface ready for further treatment.
Benefits of Sandblasting
Cleaning: Sandblasting eliminates all traces of surface impurities, ensuring a clean base for subsequent treatments.
Surface Roughness: It allows for precise control over surface texture, which enhances the adherence of coatings and electroplating materials.
Mechanical Properties: By smoothing out surface imperfections, sandblasting improves the overall flatness of machined parts, thereby extending machinery lifespan and performance.
Advantages of Sandblasting for Anodized Aluminum Alloy
The matte finish achieved through sandblasting offers both aesthetic and functional advantages. In environments where reflective surfaces are undesirable, such as certain industrial settings, sandblasted aluminum profiles provide a subtle, elegant appearance while effectively concealing extrusion lines and minor imperfections. Moreover, the process ensures that the surface is thoroughly prepared for anodizing by removing any residual oxide films.
Applications and Industries
Sandblasted aluminum profiles find application across diverse industries, including architecture, automotive manufacturing, aerospace, and electronics. These sectors benefit from the enhanced durability and aesthetic versatility offered by sandblasted finishes, particularly in applications where both performance and visual appeal are paramount.
Technological Insights
Recent advancements in sandblasting technology have streamlined the process, incorporating automated systems and environmentally friendly abrasive materials. These innovations not only improve efficiency and precision but also align with sustainable manufacturing practices, reducing environmental impact.
Conclusion
In conclusion, sandblasting plays a critical role in preparing aluminum alloy products for anodizing, enhancing both their functional properties and visual appeal. As industries continue to demand high-performance materials with superior aesthetic qualities, the importance of effective surface preparation methods like sandblasting remains indisputable.
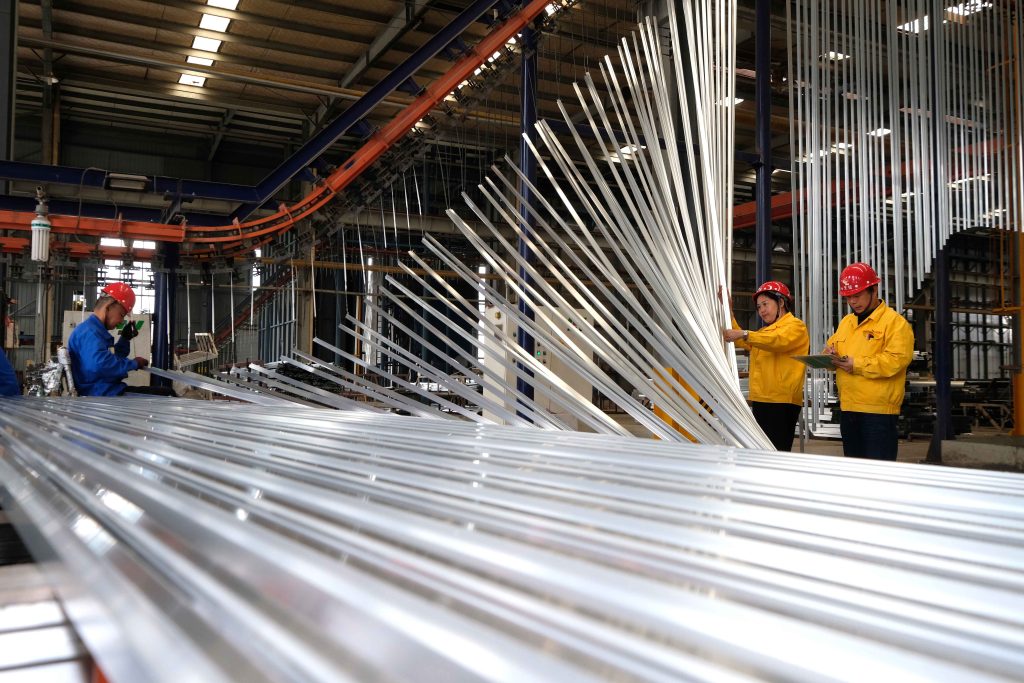