Rina takes you on today’s journey together
Hey there, aluminum enthusiasts! Rina Meng here, ready to dive into the fascinating world of aluminum alloy products and their sandblasting adventures. Today, we’re exploring the burning question: why in the world do these products need a good sandblasting before oxidation? Buckle up, my friends, because we’re about to embark on a wild ride of sand, particles, and smooth surfaces!
Let’s start with the basics, shall we? The principle behind sandblasting aluminum alloy products is simple yet powerful. We take those high-speed sand particles and let them go wild on the surface of the aluminum alloy. Their mission? To obliterate the oxide layer and any pesky dirt that might be hanging around. It’s like giving your aluminum alloy product a spa day, making the surface smoother and more fabulous than ever before. But wait, there’s more!
Before the product goes through the magical process of oxidation, it needs a little prep work. Think of it as getting ready for a glamorous night out. The aluminum alloy product goes through some cleaning and degreasing, making sure it’s all spick and span. We want that surface to be pristine, my friends! And that’s where sandblasting comes in, like a superhero swooping in to save the day.
Now, let’s talk benefits, because sandblasting is all about the perks, baby! First up, cleanliness. Sandblasting is like the ultimate cleaning machine, wiping away all the dirt, scale, and dust that dare to cling to the surface of the workpiece. It’s like giving your aluminum alloy product a refreshing shower, leaving it squeaky clean and ready to shine.
But wait, there’s more! Sandblasting also has this nifty trick up its sleeve—it can increase the surface roughness. Yeah, you heard me right. It’s like giving your aluminum alloy product a little texture, adding a touch of personality. Plus, this roughness comes in handy when it’s time for electroplating. It’s like the perfect matchmaker, bringing the aluminum alloy shell and the plating materials together in holy matrimony. Talk about a match made in aluminum heaven!
And that’s not all, folks. Sandblasting works its magic on the mechanical properties of aluminum alloy shells too. After the sandblasting extravaganza, those aluminum profile machinery parts become smooth oil magnets. They store that smooth oil in tiny micro pits on the surface, making everything flat and fabulous. It’s like giving your machinery a spa day, extending its service life and keeping it running like a well-oiled machine. Pun intended!
Now, let’s get down to the nitty-gritty of the sandblasting process itself. Picture this: your aluminum alloy product enters the sandblasting machine, ready for some high-speed sand action. It’s like a thrilling rollercoaster ride, but instead of loops and drops, it’s all about sand particles impacting the surface. Once the sand has done its job, it’s time for a dip in the cleaning tank. We want to make sure all the remaining sand and dirt are washed away, leaving the surface sparkling clean.
Last but not least, we give our aluminum alloy product a good drying session. We want that surface to be as dry and smooth as a baby’s bottom. It’s like the final touch, sealing the deal and getting that product ready for the next step in its aluminum adventure.
Now, my dear readers, let’s talk about what makes a sandblasting product truly qualified. We have some standards to uphold, after all! A qualified sandblasting product is allowed to have a few imperfections. We’re talking about rust, dirt, marks, blooms, and even a little floating sand. It’s like giving the product a touch of character, a story to tell. But of course, we have limits. We don’t want visible deformation or bruising. Let’s keep it classy, folks!
Now, let’s get to the juicy part—the advantages of sandblasting oxidized aluminum alloy. First up, the matte factor. Sandblasting gives aluminum profiles a subdued and understated feel. It’s like taking a step back from the flashy and embracing the more sophisticated side of things.
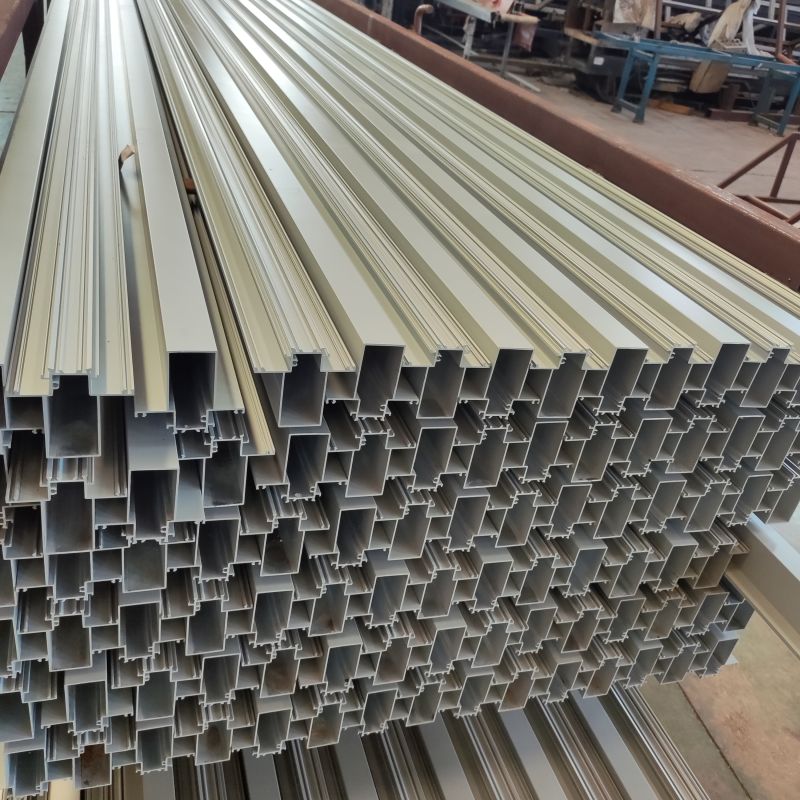