Rina takes you on today’s journey together
Hey there, aluminum enthusiasts! Rina Meng here, your go-to gal for all things aluminum profiles. Today, I want to dive into the fascinating realm of oxidation and shed some light on the difference between hard oxidation and its ordinary counterpart. Buckle up, because we’re about to embark on an aluminum adventure like no other!
Picture this: you’re strolling through a bustling factory, surrounded by the clanking of machines and the sweet smell of metal in the air. Suddenly, you come across two aluminum products, both boasting a shiny oxide film. But here’s the twist—one is hard oxidized, and the other is just your run-of-the-mill ordinary oxidation. So, what sets them apart? Let’s find out!
Hard oxidation, my friends, is the cream of the crop when it comes to anodizing aluminum. It’s a special surface treatment process that creates a thick oxide film, reaching up to a whopping 250 microns in thickness. That’s like having an aluminum superhero with an extra layer of armor! This process works wonders on both pure aluminum and aluminum alloys, giving them a microhardness oxide film that can withstand the test of time.
Now, you might be wondering, “Rina, what makes this hard oxide film so special?” Well, hold onto your hats, folks, because I’m about to drop some knowledge bombs. First off, this film has superb corrosion resistance, making it the ultimate shield against the elements. Rain, wind, and even the occasional pigeon droppings—nothing can penetrate its mighty defenses!
But wait, there’s more! This film also boasts excellent wear resistance, perfect for parts that go through the ringer. Think pistons, cylinders, bearings, and even those trusty aircraft cargo compartment floors. With hard oxidation, you can bid farewell to constant replacements and say hello to durability that would make even the Hulk jealous.
Now, let’s talk about insulation. This hard oxide film is a true master of heat resistance, keeping things cool when the pressure’s on. It’s like having your own personal air conditioner for your aluminum parts! Plus, with a breakdown voltage of up to 2000V, you can rest easy knowing that your electrical components are in good hands.
“But Rina,” you might interject, “what about the regular, ordinary oxidation? Is it just a sad, second-rate version of hard oxidation?” Not at all, my friend! Ordinary oxidation still has its charms, although it might not be as flashy as its hard counterpart. When aluminum undergoes ordinary oxidation, the oxide film forms on the surface, creating a protective layer that shields it from corrosion.
The key difference is that with ordinary oxidation, the oxide film doesn’t penetrate the aluminum alloy like it does with hard oxidation. Instead, it simply adheres to the surface, making the product’s outer size smaller while keeping those inner pores nice and cozy. So, if you’re looking for a sleek and compact finish, ordinary oxidation might just be your cup of tea.
Now, let’s address the elephant in the room—why should you care about hard oxidation? Well, my dear readers, let me count the ways! First and foremost, hard oxidation gives your aluminum alloy an impressive surface hardness of around HV500. That’s harder than a diamond! Okay, maybe not that hard, but you get the idea.
The thickness of the oxide film is also worth mentioning. With hard oxidation, you can achieve a range of 25 to 250 microns, providing that extra layer of protection for your precious aluminum. And let’s not forget about the strong adhesion of the film. Half of it penetrates into the aluminum alloy, while the other half stays put on the surface, creating a bond that would make even the best buddy cop duo jealous.
But wait, there’s more! This hard oxide film is an insulation champ, with a breakdown voltage that can reach a staggering 2000V. It’s like having an electric fence around your aluminum parts, keeping unwanted currents at bay. And if you’re worried about wear and tear, fear not! Hard oxidation delivers excellent wear resistance, ensuring your aluminum parts stay in top-notch condition for years to come.
Now, you might be thinking, “Rina, this all sounds fantastic, but is hard oxidation safe for us humans?” Absolutely! The oxidation film and the electrochemical process used to create it are as harmless as a fluffy bunny. Non-toxic and environmentally friendly? Sign me up!
So, why should you consider hard oxidation for your aluminum products? Well, my friends, it’s all about versatility. By utilizing hard oxidation, you can streamline your mechanical processes, reduce product weight, and meet those ever-important environmental regulations. It’s a win-win situation, my fellow aluminum aficionados!
Overall, the difference between hard oxidation and ordinary oxidation boils down to one thing—extra oomph! With hard oxidation, you get a thick oxide film that’s tougher than nails, providing unparalleled protection, insulation, and wear resistance. Ordinary oxidation, on the other hand, offers a sleek and compact finish, perfect for those who prefer a more refined aesthetic.
So, there you have it, folks—a crash course in the marvelous world of aluminum oxidation. I hope you’ve enjoyed this wild ride as much as I have! Remember, when it comes to aluminum, the possibilities are endless. Whether you choose hard oxidation or ordinary oxidation, rest assured that your aluminum products will shine brighter than a shooting star.
Thanks for joining me on this aluminum adventure, my lovely readers! Until next time, keep shining bright and may your aluminum dreams never tarnish. Catch you on the flip side, aluminum aficionados!
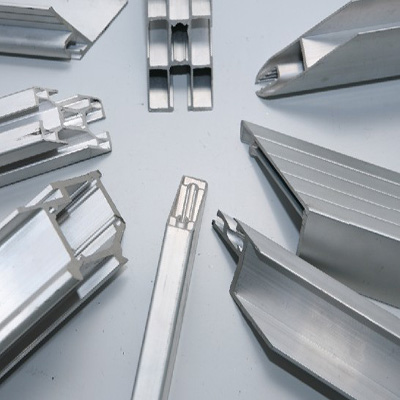