Follow in the footsteps of Rina, take you to know more aluminum profile products
Hey there, fellow aluminum enthusiasts! Today, I want to dive into the fascinating world of 7 series aluminum materials. Buckle up and get ready for a wild ride through the classification and application fields of these shiny wonders. Trust me, you’re in for a treat!
Now, before we embark on this aluminum adventure, let me give you a quick rundown of the 7 series aluminum. This series is primarily composed of zinc, but sometimes we sprinkle in a bit of magnesium and copper for that extra pizzazz. Picture it like a secret recipe for aluminum awesomeness!
One thing that sets the 7 series apart is its superhard aluminum alloy, which boasts a concoction of zinc, lead, magnesium, and copper. This alloy is so tough, it’s almost as hard as steel! Talk about an aluminum alloy with an attitude. But wait, there’s more! The extrusion speed of 7 series alloys may be slower than their 6 series counterparts, but their welding performance is top-notch. It’s like they’re saying, “Hey, we might take our time, but when it comes to welding, we’re the best in the biz!”
Now, let’s talk about where these bad boys shine—literally! The 7 series aluminum materials find their calling in the aviation industry. We’re talking about load-bearing components of aircraft, landing gear, rockets, and even aviation spacecraft. These aluminum wonders are the unsung heroes of the skies, keeping us soaring high and safe.
But hold on tight, because we’re not done yet! Let’s take a closer look at some specific members of the 7 series family and their applications. Brace yourself for a whirlwind tour of aluminum excellence!
First up, we have 7005 extruded materials. These babies are perfect for manufacturing welded structures that require both high strength and high fracture toughness. Think trusses, rods, and containers for transportation vehicles. Oh, and did I mention they also find their way into sports equipment like tennis rackets and softball bats? Talk about versatility!
Next on the list is 7039. These aluminum champs are the go-to for freezing containers, cryogenic equipment, storage boxes, fire-fighting pressure equipment, military gear, and even armor plates. They’re like the superheroes of aluminum, ready to withstand extreme conditions and protect us from harm.
Now, let’s give a round of applause to 7049. These forging parts possess the same static strength as the 7079-T6 alloy but with an added bonus: high resistance to stress corrosion cracking. They find their purpose in aircraft and missile parts, like landing gear hydraulic cylinders and extrusions. Plus, their fatigue properties are on par with the 7075-T6 alloy, making them a reliable choice for demanding applications.
Moving right along, we have the mighty 7050. These aluminum warriors are all about aircraft structural parts. When it comes to manufacturing medium and thick plates, extrusions, free forgings, and die forgings, 7050 is the name of the game. They boast high resistance to spalling corrosion, stress corrosion cracking, fracture toughness, and fatigue resistance. In other words, they’ve got it all!
Let’s not forget about the legendary 7072. This aluminum superstar takes the stage as the go-to choice for air conditioner aluminum foil and extra thin strips. But wait, there’s more! We have a whole lineup of alloys, including 2219, 3003, 3004, 5050, 5052, 5154, 6061, 7075, 7475, and 7178, which find their place in alloy plates and pipe coatings. It’s like a colorful cast of characters coming together to create aluminum magic!
Now, let’s give a standing ovation to the one and only 7075. This aluminum powerhouse is the rockstar of aircraft structures and futures. When it comes to high-strength, corrosion-resistant, high-stress structural parts, and mold manufacturing, 7075 is the king of the hill. It’s the aluminum equivalent of a superhero cape!
But wait, there’s more! We can’t forget about 7175. These aluminum wonders are all about forging high-strength structures for aircraft. The T736 material takes the cake with its excellent comprehensive properties, including high strength, resistance to spalling corrosion and stress corrosion cracking, fracture toughness, and fatigue strength. It’s like the Swiss Army knife of aluminum alloys!
Last but certainly not least, we have 7475. These aluminum-clad and non-aluminum-clad plates are the go-to choice for fuselage, wing frames, stringers, and other parts that demand both high strength and high fracture toughness. They’re the unsung heroes of aerospace engineering, silently working their magic behind the scenes.
And there you have it, folks! A whirlwind tour of the classification and application fields of 7 series aluminum materials. It’s truly mind-boggling to see the incredible range of applications these shiny wonders find themselves in.
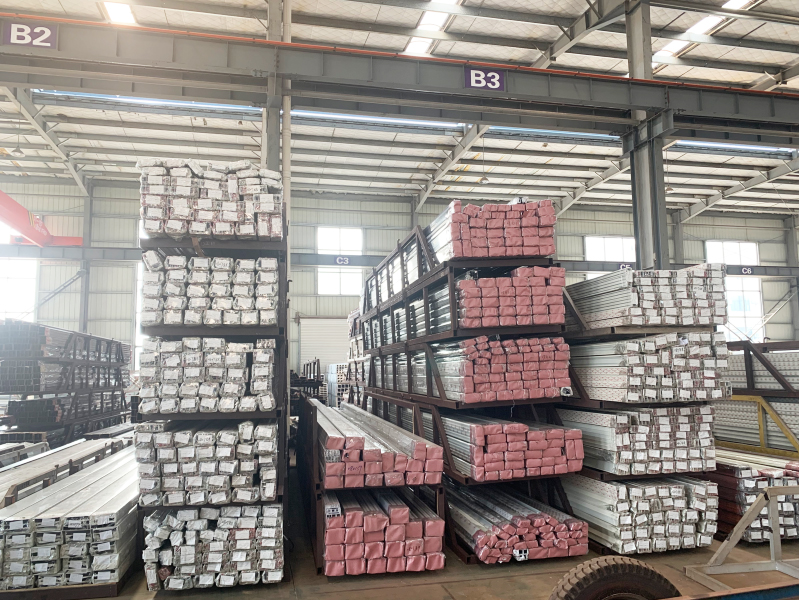