Follow in the footsteps of Rina, take you to know more aluminum profile products
Hey there, folks! Rina Meng here, your friendly neighborhood aluminum aficionado. Today, I want to talk about a topic that’s sure to give you chills (in a good way, of course). We’re diving into the fascinating world of aluminum and its application in the refrigeration industry. I mean, who knew aluminum could be so cool? Pun intended!
Now, before we get into the nitty-gritty, let me throw in a personal anecdote to break the ice. Picture this: it’s a scorching summer day, and I’m desperately seeking refuge from the relentless heat. I swing open the door of my refrigerator, and a wave of cool air washes over me like a refreshing breeze on a tropical island. Ah, pure bliss! Little did I know that aluminum played a significant role in making this cooling magic happen.
You see, my friends, aluminum has been making waves in the refrigeration industry for quite some time now. With its low density and soft texture, it’s like the superhero of metals, ready to save the day. It can be easily molded into various aluminum alloy profiles, which possess impressive mechanical and physical properties. And let’s not forget about its excellent thermal conductivity and high specific strength. It’s like aluminum was tailor-made for the refrigeration industry!
One of the areas where aluminum has truly shone is in automobile air conditioners. Yep, you heard me right—cars and air conditioners go hand in hand, like peanut butter and jelly. Aluminum has been cooling our car rides for over three decades now. Condensers, evaporators, and even radiators have embraced the aluminum revolution, all in the name of lightweight design. And who doesn’t love a lightweight car that zips through the streets with ease?
When the Ozone Layer Protection Initiative came knocking in the 1990s, aluminum stepped up its game even further. The introduction of R134a refrigerant meant that automotive air conditioners needed to up their efficiency. That’s where aluminum’s stellar heat exchange properties came into play. The brazed microchannel heat exchanger, with its 30% higher heat exchange efficiency, became the star of the show. It quickly became the go-to choice for R134a automotive air conditioners, stealing the spotlight from traditional finned tubes.
But wait, there’s more! In our quest for greener and more energy-efficient vehicles, aluminum has become the go-to material for air conditioner parts. Swash plate compressors, found in traditional fuel vehicle air conditioners, have embraced lightweight aluminum alloy materials for their casings, pistons, and swash plates. And in the world of electric vehicles, aluminum takes center stage once again. The casing, static plate, and moving plate of electric scroll compressors are all crafted from aluminum alloy materials. It’s like aluminum is the VIP guest at the air conditioning party!
Now, let’s shift gears and talk about refrigerators. These trusty appliances have been a staple in our homes for ages. And guess what? Aluminum has been making its mark here too. Back in the early 2000s, as copper prices skyrocketed, refrigerator companies started looking for alternatives. That’s when aluminum stepped in, ready to take on the challenge.
Aluminum turned out to be the perfect substitute for copper in refrigerators. Sure, it may not have the same thermal conductivity as copper, but it’s no slouch either. With some clever heat exchanger design tweaks, aluminum can hold its own against copper in terms of heat exchange performance. Plus, aluminum has a few tricks up its sleeve. It’s highly processable, abundant, and more cost-effective than copper. Talk about a win-win situation!
Today, you’ll find aluminum playing a starring role in the refrigeration pipeline of most mainstream refrigerator companies. Copper pipes have taken a step back, making way for a combination of copper and aluminum. The compressor connecting pipe, return pipe, and evaporator—all crafted from aluminum—are the true heroes of the cooling process. Of course, we can’t forget about the capillary tubes and some connecting parts that still retain copper. But fear not, my friends, because the solution of “aluminum replacing copper” for capillary tubes is already in the works. Welding technology and new connection sealing processes are paving the way for a copper-free future.
While the application of aluminum in refrigerators has reached a mature stage, the research and development game is still going strong. We’re constantly pushing the boundaries of what aluminum can do. Special-shaped pipes, internally toothed pipes, and threaded pipes are all getting an upgrade. And let’s not forget about the holy grail of refrigeration—the efficient microchannel heat exchangers. They’re the future, my friends!
So, there you have it, folks—a glimpse into the incredible world of aluminum in the refrigeration industry. From automotive air conditioners to trusty refrigerators, aluminum has proven time and time again that it’s the real MVP. It cools us down, lightens our loads, and keeps things running smoothly. What more could we ask for?
Overall, I’m in awe of the versatility and ingenuity of aluminum in the refrigeration industry. It’s a testament to human innovation and our never-ending quest for improvement. So, the next time you open your refrigerator or hop into your air-conditioned car, take a moment to appreciate the cool breeze and the aluminum magic that makes it all possible.
Thanks for joining me on this aluminum adventure, folks! Remember, stay cool, stay curious, and keep embracing the aluminum revolution. Until next time, catch you on the flip side!
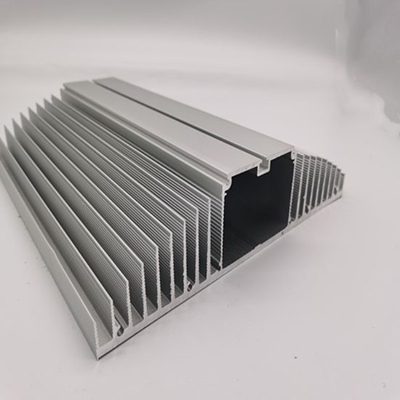