Rina takes you on today’s journey together
Hey there, fellow aviation enthusiasts and aluminum aficionados! Today, I want to dive into the fascinating world of aluminum stamping parts in the aerospace industry. Buckle up and prepare for a wild ride as we explore what these parts are all about and uncover the factors that can affect their costs. So, fasten your seatbelts and let’s take off!
Picture this: you’re soaring through the sky, gazing out of the window at the magnificent wings and sleek fuselage of the aircraft. Those impressive structural components are often made using aluminum stamping parts. Why, you ask? Well, my friend, aluminum is like the superhero of materials—it’s lightweight, strong, and corrosion-resistant. It’s like having a combination of Iron Man, Wonder Woman, and Captain America all rolled into one!
These aluminum stamping parts work their magic in various areas of the aircraft. For starters, they play a crucial role in the production of structural components like wing panels, fuselage sections, and landing gear. By harnessing the power of aluminum, these parts enhance aircraft performance and fuel efficiency. It’s like giving the plane a turbo boost while sipping on a refreshing energy drink!
But wait, there’s more! Aluminum stamping parts also strut their stuff in the interior components of the aircraft. Think seat frames, cabin partitions, air conditioning ducts, cabinetry, and even lavatory components. These parts are designed to be lightweight and strong, ensuring the comfort and safety of passengers. Plus, those aluminum cabin partitions not only provide structural support but also give the cabin a sleek and modern look. Talk about multitasking!
Now, let’s not forget about the engine components. Aluminum stamping parts are the unsung heroes in this area too. They lend their strength and corrosion-resistant nature to engine mounts, turbine blades, exhaust systems (like exhaust cones and nozzles), and fuel system components (such as fuel tanks and fuel lines). These parts need to withstand the intense heat, pressure, and harsh environments of the engine. Aluminum stamping parts are like the tough bodyguards protecting the heart and soul of the aircraft!
And guess what? Avionics components also get in on the aluminum action. Instrument panels, antenna brackets, radar equipment (including radar domes and mounting brackets), electrical components (like circuit boards and connectors), and communication equipment—all of them find their home on aluminum stamping parts. Aluminum’s excellent electromagnetic shielding properties make it the perfect shield against interference. It’s like having a force field to protect the delicate electronics. How cool is that?
Now that we’ve explored the exciting world of aluminum stamping parts in the aerospace industry, let’s shift gears and talk about the factors that can affect their costs. Brace yourself for some turbulence as we navigate through these cost-affected factors!
First up, we have material cost. The type and grade of aluminum used can influence the price tag. Higher-grade aluminum alloys may be pricier, but they offer better strength, durability, and corrosion resistance. It’s like choosing between a fancy sports car or a trusty sedan—both get the job done, but one might have a bit more oomph!
Next, we have production volume. This one’s a classic case of “the more, the merrier.” Larger production runs often lead to lower costs per part. It’s like buying in bulk at your favorite warehouse store—you get more bang for your buck! On the other hand, smaller production runs may come with a higher price tag per part. So, it’s all about finding that sweet spot between quantity and quality.
Ah, tooling costs—a formidable factor that can make or break the budget. Creating aluminum stamping parts requires specialized tooling, like dies and molds. The complexity of the part, the number of pieces needed, and the type of tooling required can all impact the cost. It’s like assembling a puzzle—some pieces are trickier to fit together, and the tools needed to make them can be more expensive. But hey, the end result is totally worth it!
Now, let’s talk about design complexity. Just like in fashion, intricate designs can add a touch of elegance and sophistication to aluminum stamping parts. However, they can also bump up the cost. Parts with fancy shapes, curves, or features might require more complex tooling or additional production steps. It’s like crafting a work of art—it takes time, skill, and sometimes a few extra bucks to bring that masterpiece to life.
Hold on tight, because we’re about to land on the topic of surface finish. Some aluminum stamping parts require a high-quality finish, like polishing or painting. These extra steps can drive up the cost. It’s like getting a manicure or a fresh coat of paint on your car—it’s all about that flawless finish. So, if you want your parts to shine brighter than a shooting star, be prepared to invest a little extra.
Quality requirements also play a role in the cost of aluminum stamping parts. Parts that demand tighter tolerances, higher strength, or special features may require additional processing or inspection steps. It’s like going the extra mile to ensure top-notch quality. After all, we want these parts to perform flawlessly and keep our aircraft soaring through the skies with confidence!
Last but not least, we have industry regulations. The aerospace industry has strict standards and regulations that must be met. Compliance with these regulations may involve additional testing, certification, or documentation, all of which can increase the cost. It’s like passing through a security checkpoint at the airport—they want to make sure everything is safe and sound before you take flight.
Overall, aluminum stamping parts are the unsung heroes in the aerospace industry. They bring their lightweight, high-strength, and corrosion-resistant powers to various components, from structural elements to avionics and engine parts. But when it comes to their costs, factors like material, production volume, tooling, design complexity, surface finish, quality requirements, and industry regulations can all come into play.
Phew! We’ve covered a lot of ground today, my fellow aluminum enthusiasts. I hope this journey through the world of aluminum stamping parts in the aerospace industry has left you feeling enlightened and entertained. Remember, the sky’s the limit when it comes to the possibilities of aluminum!
Now, as we prepare to disembark, I want to thank you for joining me on this adventure. It’s been a pleasure having you on board! Until we meet again, keep reaching for the stars, stay curious, and always remember: aluminum stamping parts are the real MVPs of the aerospace industry. Catch you on the flip side, my friends!
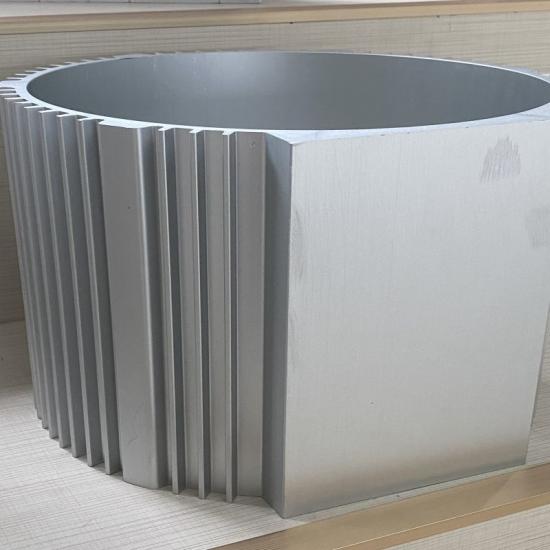