Follow Rina to show you more information about aluminum profiles
Hey there, fellow car enthusiasts! Buckle up and get ready for a wild ride as we dive into the world of aluminum alloys in the automotive industry. Today, I want to talk to you about the durability of 6061 aluminum forgings and how they play a crucial role in ensuring the safety and reliability of our beloved automobiles. So, let’s hit the road and explore the fascinating world of 6061 aluminum!
Now, before we get into the nitty-gritty details, let me give you a quick rundown on why aluminum is the go-to material for car manufacturers. Picture this: a lightweight and robust material that can significantly reduce the weight of vehicles, leading to improved fuel efficiency and reduced emissions. Sounds like a dream, right? Well, my friends, that dream is a reality, and it goes by the name of aluminum alloy.
Among the various aluminum alloys out there, 6061 aluminum steals the show when it comes to automotive parts. This alloy is a superstar in terms of its mechanical properties, corrosion resistance, and weldability. It’s like the Beyoncé of aluminum alloys—strong, flexible, and always ready to slay!
When we talk about durability, we’re talking about the ability of automotive parts to withstand the test of time and keep us safe on the road. The durability of 6061 aluminum forgings is determined by a bunch of factors, such as tensile strength, yield strength, elongation, and hardness. According to the Aluminum Association, 6061-T6 aluminum forgings boast some impressive numbers: a jaw-dropping ultimate tensile strength of 290 MPa, a yield strength of 240 MPa, an elongation of 8%, and a Brinell hardness of 95. These properties are on par with, or dare I say, even better than those of other automotive materials like steel, titanium, and magnesium. Take that, heavyweights!
But hold on, my friends, durability isn’t just about mechanical properties. It’s like a multi-layered cake with various delicious flavors. In the case of 6061 aluminum forgings, their ability to withstand environmental factors like corrosion, fatigue, and impact is what adds that extra oomph to their durability.
Corrosion, the arch-nemesis of metallic materials, can wreak havoc on our precious automotive parts. But fear not! 6061 aluminum forgings come prepared with a natural oxide film on their surface, acting like a superhero shield against corrosion. They can stand tall against atmospheric agents, water, and even chemical attacks. So, whether you’re driving through salt spray, acid rain, or hot and humid conditions, these forgings will keep their structural integrity and aesthetic appeal intact. Talk about a tough cookie!
Now, let’s talk about fatigue. No, I’m not talking about that feeling you get after a long day of work. I’m talking about the gradual accumulation of damage caused by repeated cyclic loading, which can lead to part failure. But fear not, my friends, for 6061 aluminum forgings have a secret weapon—forging process optimization! By tinkering with factors like temperature, pressure, and deformation rate, we can create forgings with a refined and homogeneous microstructure. This fancy microstructure enhances their fatigue strength and crack resistance, making them last longer than your favorite pair of worn-out jeans. And if that’s not enough, we can also treat these forgings with techniques like shot peening, laser shock peening, and anodizing, which take their fatigue performance to a whole new level. It’s like giving them a superhero upgrade!
Last but not least, let’s talk about impact resistance. Our cars face all sorts of impact loads—bumps, potholes, collisions, and vibrations—during their lifetime. It’s like they’re in an action movie, constantly dodging danger! The impact resistance of 6061 aluminum forgings comes down to their ductility, which is their ability to deform without fracturing. The 6061-T6 temper strikes the perfect balance between strength and ductility, making it suitable for most automotive applications. But here’s a word of caution: in extreme cases like high-speed impacts or severe crashes, these forgings may reach their ultimate strength and fracture. That’s why it’s crucial to design the automotive structure and components to absorb and distribute the impact energy, rather than relying solely on the material toughness. Safety first, folks!
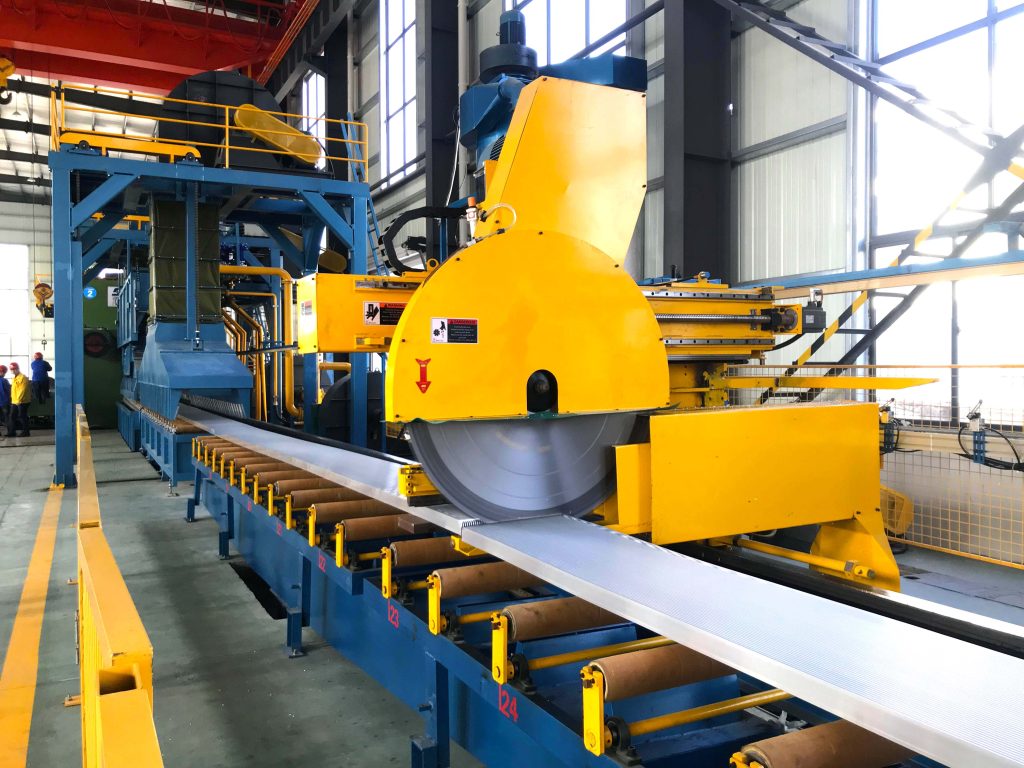