Introduction
In the realm of aluminum product processing, surface oxidation stands out as a vital treatment process. Naturally, aluminum and its alloys form an oxide film when exposed to the atmosphere. However, these naturally formed films are often insufficient for reliable protection or decoration.
The Evolution of Aluminum Surface Treatment
The aluminum product processing industry has evolved significantly, increasingly adopting anodizing and chemical oxidation methods. These techniques are instrumental in generating protective and decorative oxide films on aluminum surfaces.
Chemical Oxidation versus Anodizing
While chemical oxidation creates oxide films typically ranging from 0.3 to 4µm in thickness, these films lack the durability and wear resistance of anodized films. On the other hand, anodizing produces a thicker film (5-20µm), offering enhanced protection and decoration. Chemical oxidation is rarely used alone due to its limited wear resistance but is highly effective in improving corrosion resistance when used in conjunction with other treatments.
Characteristics of Anodized Films
Anodized films on aluminum boast several key properties: enhanced corrosion resistance, strong adsorption capacity, excellent insulation, and high hardness. These characteristics significantly elevate the functional and aesthetic quality of aluminum products.
Corrosion Resistance of Anodized Films
The corrosion resistance of anodized films varies between pure aluminum and aluminum alloys. Due to the presence of non-oxidizable metal compounds in alloys, the oxide film can become discontinuous, necessitating sealing to improve corrosion resistance.
Adsorption Capacity and Decorative Applications
Anodized films have a porous structure, endowing them with a strong adsorption capacity. By filling these pores with various pigments, lubricants, or resins, the protective, insulative, wear-resistant, and decorative qualities of aluminum products are significantly enhanced.
Insulation Properties of Anodized Films
Post-anodization, aluminum transforms from a conductive metal to an excellent insulating material, expanding its application scope.
Hardness and Wear Resistance
The hardness of anodized films varies, generally being higher in pure aluminum. The anodized film’s surface layer, capable of absorbing lubricants, further improves wear resistance, making it ideal for applications requiring durability.
Conclusion
Advanced surface treatment processes like anodizing and chemical oxidation have revolutionized the aluminum industry. These treatments not only protect aluminum products but also enhance their aesthetic appeal and functional capabilities, marking a significant stride in material science.
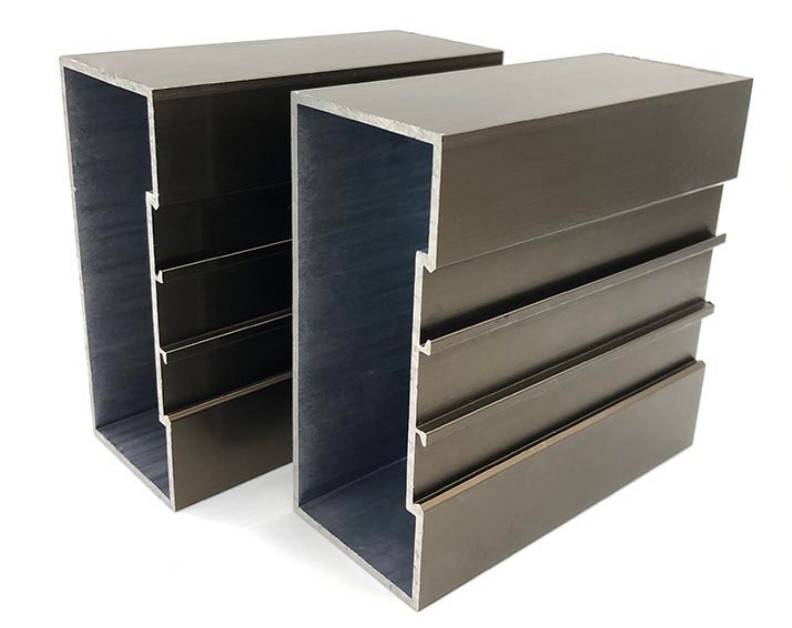