Introduction to Heat Sink Aluminum
Heat sink aluminum is a critical component in various technological and industrial applications, playing an essential role in thermal management systems. Its popularity stems from its exceptional ability to conduct heat, making it an ideal choice for dissipating heat from electronic devices and other machinery. The significance of heat sink aluminum lies in its ability to maintain optimal operating temperatures, thus enhancing the longevity and efficiency of devices. In a world where electronic devices are becoming increasingly compact yet powerful, the demand for effective heat dissipation solutions like heat sink aluminum has surged. This article aims to delve into the intricacies of heat sink aluminum, exploring its properties, types, manufacturing processes, and applications across diverse industries. The use of heat sink aluminum is a testament to its versatility and effectiveness in tackling the challenges posed by heat generation in modern devices and machinery.
Properties and Types of Aluminum for Heat Sinks
Aluminum heat sinks, known for their high thermal conductivity and low strength, are essential in thermal management solutions. Different grades of aluminum, such as 6063, 6061, 6060, and 1050, are used in producing heat sinks, each offering unique features and benefits. For instance, 6063 aluminum is preferred for its excellent extrudability and surface finish, making it ideal for aesthetic applications where appearance matters. On the other hand, 6061 aluminum offers a balance of strength, corrosion resistance, and weldability, suitable for more robust applications. These variations in aluminum grades allow manufacturers to tailor heat sink solutions to specific requirements, ensuring optimal heat dissipation. The choice of aluminum grade impacts the overall performance of the heat sink, influencing factors such as thermal efficiency, weight, and durability. Understanding the distinct properties of these aluminum grades is crucial for selecting the right heat sink aluminum for any given application.
Applications in Various Industries
The application of heat sink aluminum spans multiple industries, underlining its versatility and importance. In the aerospace sector, heat sink aluminum is crucial for managing the thermal loads of aircraft electronics, ensuring safety and functionality. In the medical field, it plays a vital role in keeping critical diagnostic and treatment equipment cool. The automotive industry utilizes heat sink aluminum in vehicle electronics, where maintaining optimal temperatures is crucial for performance and safety. In the realm of electronics, heat sink aluminum is indispensable in dissipating heat from CPUs, GPUs, and other high-performance components. Its use in solar thermal water systems and geothermal cooling and heating highlights its efficiency in renewable energy applications. These varied applications showcase the adaptability of heat sink aluminum, making it an essential material in modern technology and innovation.
Aluminum vs. Copper Heat Sinks
When comparing aluminum and copper heat sinks, several key factors come into play. Although copper heat sinks possess higher thermal conductivity, aluminum heat sinks are more popular due to their cost-effectiveness and lightweight nature. The choice between aluminum and copper often hinges on specific application requirements and budget constraints. Aluminum, being lighter, is advantageous in applications where weight is a critical factor, such as in aerospace or portable electronic devices. Copper, while offering superior heat dissipation, is heavier and more expensive, making it less suitable for applications where cost and weight are significant considerations. The decision to use aluminum or copper heat sinks involves a careful analysis of thermal requirements, weight constraints, and budget limitations. This comparison highlights why aluminum is the preferred material for heat sinks in a wide range of applications, offering a balanced solution between performance, cost, and weight.
The Manufacturing Process and Working of Aluminum Heat Sinks
The manufacturing process of aluminum heat sinks varies, including methods like extrusion, skiving, bonding, die casting, and CNC machining. Each method caters to different design and performance requirements, influencing the heat sink’s efficiency in dissipating heat. The working process of aluminum heat sinks involves several key steps: generating heat from a source, transmitting heat away from the source, distributing the heat evenly across the heat sink, and finally dissipating the heat into the surrounding environment. This process is essential in maintaining the optimal functioning of electronic devices and machinery, preventing overheating and potential damage. The manufacturing method and design of the heat sink play crucial roles in its effectiveness, determining how well it can manage the thermal load of the device it is attached to. Understanding these manufacturing processes and the working mechanism of heat sinks is vital for anyone involved in designing or using thermal management solutions.
Conclusion
In conclusion, heat sink aluminum is an indispensable material in the world of thermal management. Its applications across various industries, from aerospace to electronics, demonstrate its versatility and effectiveness in dealing with heat dissipation challenges. The choice of aluminum over other materials like copper is often driven by factors such as cost, weight, and specific application requirements. As technology continues to advance, the role of heat sink aluminum in managing the thermal loads of increasingly powerful and compact devices becomes ever more crucial.
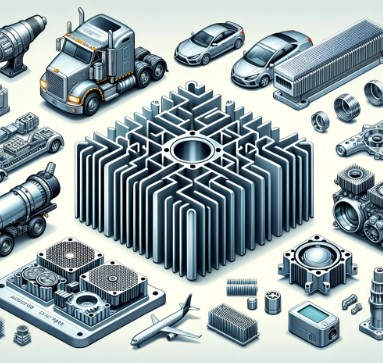