Aluminum in Aerospace: Elevating Safety and Efficiency in Modern Aviation
The aerospace industry has long recognized aluminum as a cornerstone material, pivotal to the development of aircraft and space exploration vehicles. From the Wright brothers’ first flight to the sophisticated spacecraft of today, aluminum alloys have been instrumental in pushing the boundaries of what’s possible in aviation and beyond.
Aluminum’s Early Contributions to Aviation
The journey of aluminum in aviation began when the industry moved away from wood and fabric to more durable and lighter materials. Aluminum’s inherent properties, such as its high strength-to-weight ratio and resistance to corrosion, revolutionized aircraft design and performance. The use of aluminum alloys was a key factor that enabled the first airplanes to soar into the sky, marking the dawn of modern aviation.
Aluminum Alloys in Aircraft Design
In the realm of commercial aircraft, aluminum alloy panels have become a staple for their complexity and performance requirements. Iconic aircraft like the Airbus A340 and Boeing 777 owe much of their structural integrity and efficiency to aluminum. This material offers a blend of durability and resistance to various forms of corrosion, making it ideal for the high-stakes environment of aerospace engineering.
The Evolution of Aerospace Aluminum Alloys
The development of aluminum alloys has been marked by several key stages, each driven by the industry’s evolving needs. Initially, the focus was on reducing weight and enhancing specific stiffness and strength. As technology and requirements advanced, the attention shifted towards improving the alloys’ durability and damage tolerance. Innovations such as the 7XXX series alloys and the introduction of aluminum-lithium hybrids have further reduced structural weight while maintaining performance stability.
Aluminum in the Space Sector
Aluminum’s role extends beyond our atmosphere, serving as the primary propellant in space shuttle solid rocket boosters and forming the structure of satellites and spacecraft. The Orion spacecraft, a symbol of NASA’s future space exploration ambitions, utilizes advanced aluminum-lithium materials to withstand the rigors of space travel.
Aluminum vs. Composite Materials
While composite materials have gained popularity for their lightweight and strong properties, aluminum continues to be indispensable in many aerospace applications. The comparison often comes down to the specific requirements of the project, with aluminum alloys frequently chosen for their proven track record in safety and reliability.
Future Trends in Aerospace Materials
As the aerospace industry continues to innovate, aluminum remains at the forefront of material research and development. The third generation of aluminum alloys, particularly aluminum-lithium, is paving the way for even lighter and stronger aircraft. These advancements promise to further enhance the efficiency and safety of both commercial and exploration vehicles.
Conclusion
Aluminum’s journey in aerospace is a testament to the material’s adaptability, resilience, and unmatched ability to meet the demands of an ever-evolving industry. As we look to the skies and beyond, aluminum alloys will undoubtedly continue to play a crucial role in shaping the future of aviation and space exploration, driving safety, efficiency, and innovation to new heights.
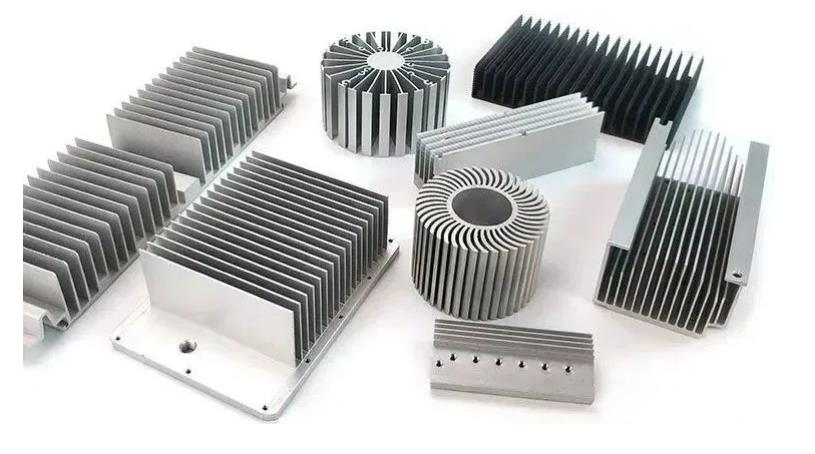