Introduction
A prevalent misconception in the industry suggests that the quality of industrial aluminum profiles is directly proportional to their thickness. Many believe that a thicker profile equates to superior quality, leading to a blind pursuit of the heftiest options available. However, this article aims to debunk this myth and provide a comprehensive guide on choosing the right aluminum profiles for specific applications, ensuring both efficiency and cost-effectiveness.
The Myth of Thickness Equals Quality
It’s a common assumption that the thicker the aluminum profile, the better its quality. This belief has led many to choose the thickest profiles available, overlooking other crucial factors. However, this approach is flawed. While thickness can contribute to the load-bearing capacity to a certain extent, it is not the sole determinant of a profile’s overall quality or suitability for a project.
Understanding Profile Thickness
Unit Weight and Cost Implications: The thickness of an aluminum profile directly impacts its unit weight and, by extension, its price. Thicker profiles mean more material per meter, leading to higher costs. This relationship between thickness, weight, and cost is crucial when planning budgets and resources for industrial projects.
Load-Bearing Capacity: Indeed, a thicker wall in an aluminum profile can enhance its load-bearing capacity, making it suitable for structures requiring high stability. However, it’s essential to balance this need with the specific demands of the project to avoid overengineering.
Application Scope: Industrial aluminum profiles come in various specifications, tailored to different stress levels and structural requirements. From light profiles suitable for minimal stress applications to heavy-duty profiles designed for substantial load-bearing, the key lies in selecting the profile that best matches the project’s needs.
Selecting the Right Profile Thickness
The selection process should begin with a thorough analysis of the structural needs of the project. Understanding the load and stress requirements helps in choosing a profile that not only supports the structure efficiently but also avoids unnecessary expenditure on overly thick profiles. This approach ensures cost-effectiveness and project efficiency.
Case Study: Shengxin Aluminum’s Perspective
Shengxin Aluminum emphasizes the importance of choosing aluminum profiles based on actual conditions rather than defaulting to the thickest option. They argue that using heavy-duty profiles for applications that don’t require such robustness results in wasted resources and increased costs. This perspective highlights the need for a thoughtful selection process that considers the specific requirements of each application.
Common Pitfalls to Avoid
When selecting aluminum profiles, common mistakes include overvaluing thickness, neglecting the project’s specific needs, and not considering the broader cost implications. These pitfalls can lead to overspending, inefficient design, and ultimately, a less effective project outcome.
Conclusion
Choosing the right thickness for industrial aluminum profiles is not about finding the thickest option but selecting the most appropriate one for the application. By understanding the relationship between thickness, weight, load-bearing capacity, and cost, project managers can make informed decisions that balance quality, efficiency, and budget. Let’s move beyond the myth that thicker always means better and towards a more nuanced approach to selecting aluminum profiles.
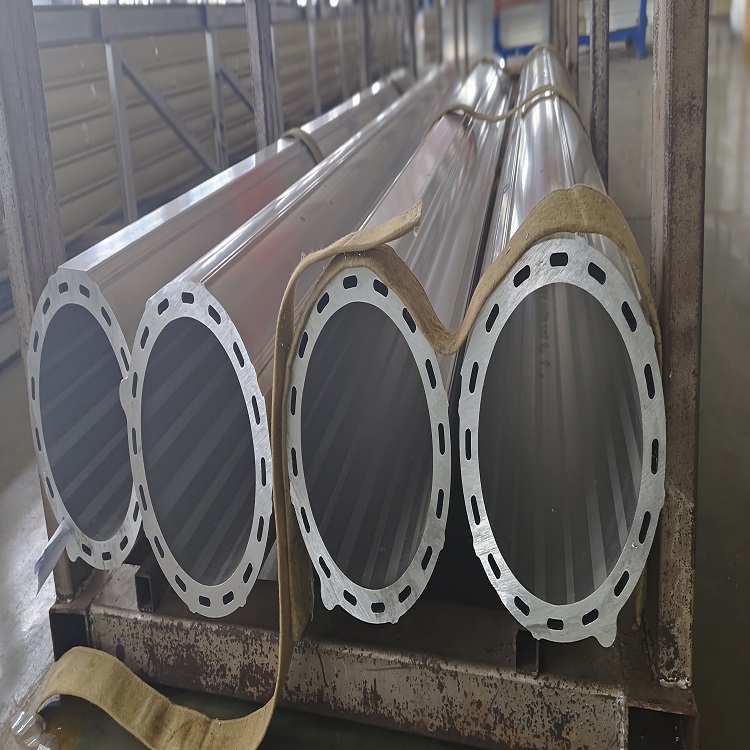