Introduction
Oxidized brushed aluminum sheets have revolutionized industries with their unique blend of durability, aesthetics, and versatility. Used extensively in manufacturing and design, these sheets offer a sophisticated solution for diverse applications.
Manufacturing Process of Oxidized Brushed Aluminum Sheets
In the meticulous process of creating oxidized brushed aluminum sheets, the aluminum undergoes precise stages: deesterification, mechanical sanding, and thorough water washing. Each step ensures the surface achieves a fine hair luster that enhances its visual appeal and durability.
Applications of Oxidized Brushed Aluminum Sheets
From lighting reflectors to automotive interiors, oxidized brushed aluminum sheets find multifaceted use. They excel in indoor and outdoor building decoration, electronic product shells, and even in the automotive industry for their modern metal finish and resilience.
Key Features of Oxidized Brushed Aluminum Sheets
These sheets boast remarkable durability, remaining unblemished even under extended outdoor exposure. Their high surface hardness not only resists scratches but also contributes to their aesthetic charm, elevating the perceived value of products they adorn.
Advantages of Pressure Processing in Aluminum Plates
Pressure processing, particularly through wire drawing, enables aluminum products to achieve desired cross-sectional shapes while enhancing their corrosion resistance and aesthetic appeal. This technique has become integral in merging fashion with functionality across various industries.
Conclusion
Oxidized brushed aluminum sheets represent a pinnacle of modern manufacturing and design. Their ability to combine durability, aesthetic appeal, and ease of processing makes them indispensable across industries, from construction to consumer electronics.
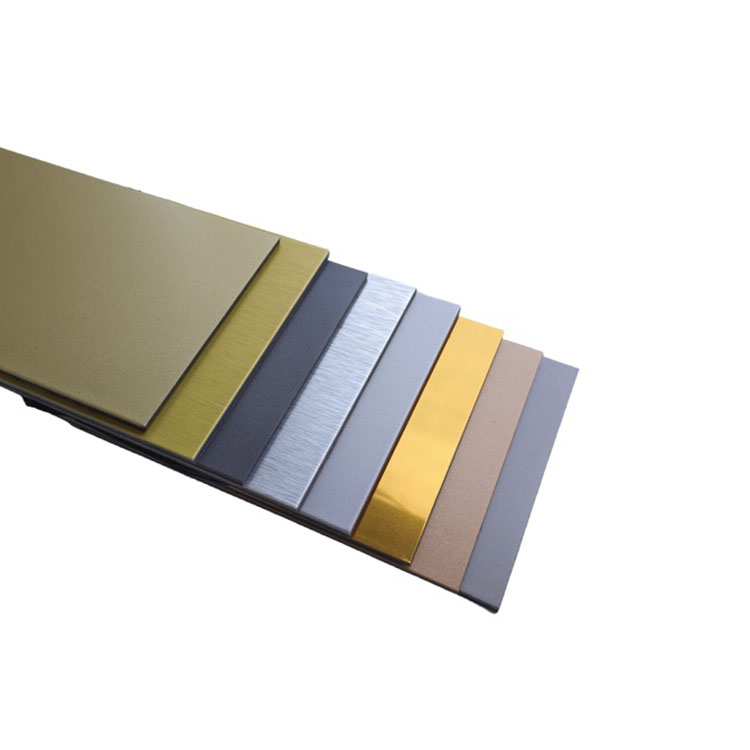