Aluminum profiles have long been integral to modern construction, valued for their lightweight nature, ease of fabrication, and robust mechanical strength. However, despite these advantages, aluminum faces challenges related to corrosion when used in its pure form or as alloys. This article explores why powder coating plays a crucial role in enhancing aluminum profiles, ensuring longevity and aesthetic appeal in architectural applications.
Introduction
Aluminum profiles are ubiquitous in contemporary architecture, employed in everything from structural frameworks to intricate facades. Their popularity stems from inherent properties such as low density and high strength-to-weight ratio, which make them ideal for building components. Yet, aluminum’s susceptibility to corrosion necessitates protective measures, particularly in outdoor environments exposed to moisture and pollutants.
Properties of Aluminum
Pure aluminum forms a natural oxide layer upon exposure to air, providing initial corrosion resistance. However, this layer, while effective, lacks the mechanical strength required for many applications. To address this limitation, aluminum alloys incorporate alloying elements like magnesium, copper, and zinc. These additions enhance mechanical properties but compromise the material’s innate corrosion resistance.
Challenges with Aluminum Alloy Profiles
The mechanical strength of aluminum alloys makes them suitable for a wide range of structural applications. However, the trade-off is reduced corrosion resistance compared to pure aluminum. This vulnerability to oxidation underscores the necessity of protective coatings, such as powder coating, to safeguard aluminum alloy profiles from environmental degradation.
Why Powder Coating is Essential
Powder coating serves as a vital protective barrier for aluminum profiles, offering superior resistance to corrosion, abrasion, and UV radiation. Unlike traditional liquid coatings, powder coating involves electrostatically applying dry powder to the substrate, which is then cured to form a durable finish. This method not only enhances durability but also allows for a myriad of color options and surface textures, facilitating seamless integration with diverse architectural styles.
Advantages of Powder-Coated Aluminum Profiles
The versatility of powder-coated aluminum extends beyond protection to aesthetic enhancement. Architects and designers appreciate the ability to specify custom colors and finishes that complement exterior wall coatings and overall building aesthetics. This adaptability ensures that powder-coated aluminum profiles blend harmoniously with the visual and functional requirements of modern construction projects.
Technological Insights
Recent advancements in powder coating technology have further improved the performance and sustainability of aluminum profiles. Innovations in powder composition and application techniques enhance adhesion, coverage, and environmental sustainability, aligning with contemporary construction practices focused on durability and eco-friendliness.
Applications
Powder-coated aluminum profiles find extensive application in architectural elements such as doors, windows, curtain walls, and cladding systems. Case studies of prominent projects illustrate how powder-coated aluminum combines functional durability with aesthetic appeal, meeting the demands of both residential and commercial building designs.
Conclusion
In conclusion, powder coating plays a pivotal role in maximizing the lifespan and performance of aluminum profiles in construction. By providing robust protection against corrosion and enabling creative design possibilities, powder-coated aluminum supports sustainable building practices while enhancing the visual impact of architectural projects. As construction trends towards durability, efficiency, and aesthetic versatility, powder-coated aluminum remains indispensable in shaping the built environment of tomorrow.
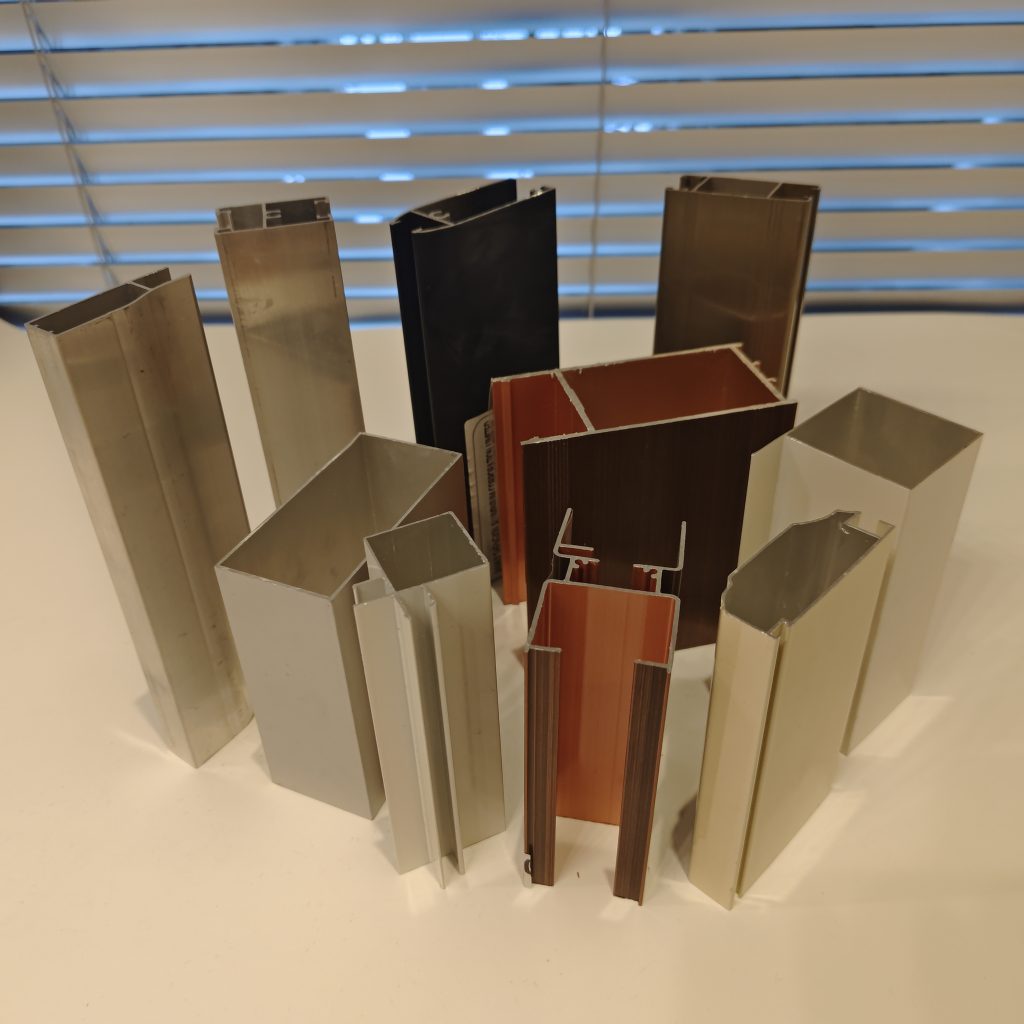