Introduction
CNC processed aluminum profiles are integral in a multitude of industrial applications. However, ensuring their quality is paramount to their functionality and longevity. This article delves into the key criteria for assessing the quality of these profiles, a necessary step for industry professionals.
Assessing Film Thickness for Corrosion Resistance
One critical aspect of quality assessment is the film thickness. This parameter is crucial for the corrosion resistance of aluminum materials. Unfortunately, to cut costs, some businesses reduce oxidation time, resulting in a thinner oxide film than required, which adversely affects the material’s corrosion resistance.
Sealing Time and Its Impact on Profile Quality
The sealing time of aluminum profiles plays a significant role in their resistance to corrosion and pollution. Shortening this time can lead to poor sealing, which, in turn, diminishes the profile’s quality and longevity. Understanding this relationship is key in quality assessment.
The Role of Equipment in Quality Control
The quality of CNC processed aluminum profiles is also dependent on the equipment used. Outdated or old extrusion machines and CNC processing equipment can result in profiles that don’t fit tightly or, worse, are unusable. Thus, modern and well-maintained equipment is crucial for high-quality output.
Importance of Wall Thickness Measurement
Another vital aspect is the wall thickness of the aluminum profile. This dimension not only impacts cost but also plays a role in meeting quality standards. Using calipers to measure wall thickness ensures that the profile falls within the acceptable tolerance range, avoiding the so-called unqualified wall thickness.
Conclusion
In conclusion, accurately assessing the quality of CNC processed aluminum profiles is crucial in various industrial applications. By focusing on film thickness, sealing time, equipment quality, and wall thickness, professionals can ensure that these profiles meet the highest standards of quality and reliability.
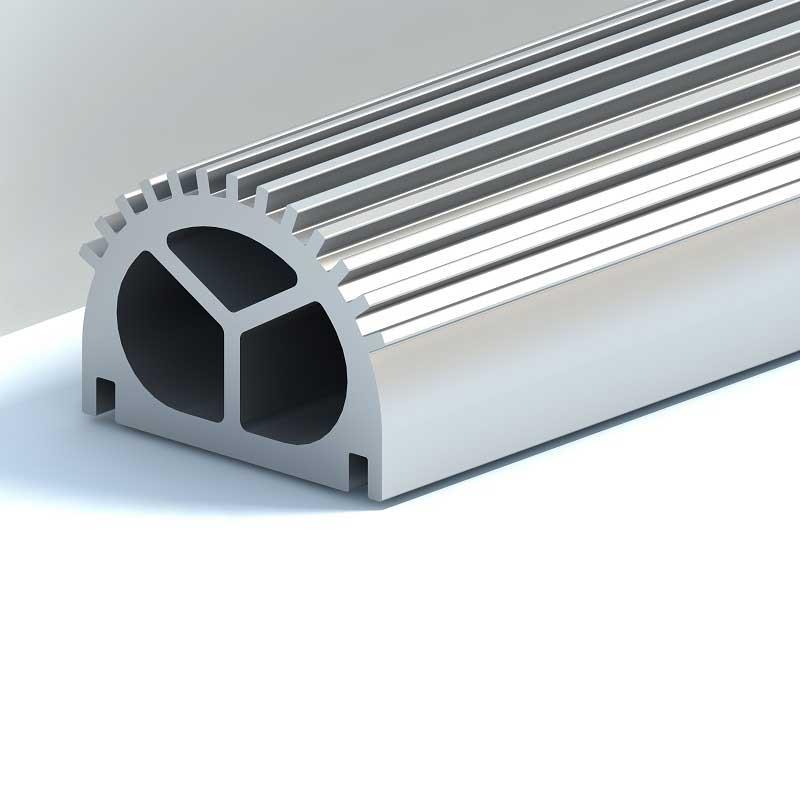