Introduction to Extruded Aluminum Profiles
Extruded aluminum profiles are foundational components in modern manufacturing, playing a pivotal role across various industries. The process of aluminum extrusion involves transforming aluminum alloy into an array of cross-sectional profiles, a technique that has evolved significantly since its inception. These profiles offer an unparalleled blend of strength and flexibility, making them ideal for diverse applications. From the frames of consumer electronics to the structural elements of skyscrapers, extruded aluminum profiles are omnipresent, testament to their versatility and reliability. Understanding their impact starts with exploring their history, a journey that reflects the evolution of industry and technology.
Types of Extruded Aluminum Profiles
Extruded aluminum profiles come in a myriad of shapes and sizes, catering to a wide range of applications and industries. According to Tri-State Aluminum, these profiles are not just limited to a standard inventory; they are customizable to meet specific needs. This versatility is echoed by Framing Technology and MISUMI, which offer a vast array of profiles, from T-slot aluminum to complex geometric shapes. These variations serve different purposes, from structural support in construction to intricate parts in the aerospace sector. The ability to tailor these profiles in terms of size, shape, and alloy composition underscores their utility in solving complex engineering challenges, thus driving innovation across sectors.
Applications Across Industries
The use of extruded aluminum profiles spans a diverse range of sectors. In the consumer domain, they are integral to gadgets and appliances, providing lightweight yet sturdy frames. The construction industry relies on these profiles for both aesthetic and structural purposes, from window frames to support beams. They are particularly crucial in aerospace and defense, where their strength-to-weight ratio is paramount. Similarly, in the automotive and marine industries, aluminum profiles contribute to vehicle light-weighting, enhancing fuel efficiency without compromising safety. This widespread applicability highlights the inherent adaptability and functionality of extruded aluminum profiles, making them indispensable in modern manufacturing and design.
Advantages of Aluminum Extrusion
The extrusion process offers several key benefits, making aluminum profiles a preferred choice in various applications. Firstly, their strength and lightweight nature allow for the creation of sturdy yet efficient designs, a critical factor in sectors like aerospace and automotive. Secondly, the flexibility of the extrusion process means that custom and complex shapes can be created to meet specific requirements, offering a level of versatility that is hard to match. Additionally, aluminum extrusion is a cost-effective manufacturing process, particularly when considering the durability and longevity of the end product. This combination of attributes – durability, versatility, and cost-effectiveness – underscores the value of extruded aluminum profiles in contemporary engineering and design.
Choosing the Right Aluminum Profile for Your Needs
Selecting the appropriate extruded aluminum profile for a specific application requires careful consideration of several factors. Size, shape, and alloy type are crucial aspects to evaluate, each impacting the performance and suitability of the profile for a given use. Expert consultation is often necessary, as providers like Tri-State Aluminum offer guidance based on extensive experience with various aluminum alloys and applications. For those requiring unique solutions, custom extrusion offers a pathway to meet specialized needs. This tailored approach ensures that the specific requirements of a project are met, whether it’s for a small consumer product or a large-scale industrial application.
Conclusion: The Future of Aluminum Extrusion
The future of extruded aluminum profiles looks bright, with continuous innovations in alloy development and extrusion techniques. The sustainability of aluminum, being recyclable without loss of quality, adds to its appeal in an environmentally conscious market. As industries evolve, the demand for more efficient, lightweight, and strong materials will further cement the role of aluminum extrusions in manufacturing. Their ability to adapt to the changing needs of technology and design signifies that extruded aluminum profiles will continue to be a cornerstone in the development of a wide array of products and structures, shaping the landscape of modern manufacturing.
FAQ Generation
FAQs About Extruded Aluminum Profiles
Q1: What are extruded aluminum profiles?
A: Extruded aluminum profiles are shapes created by pushing aluminum alloy through a die, resulting in a continuous cross-sectional profile used in various applications across industries.
Q2: What industries commonly use extruded aluminum profiles?
A: These profiles are widely used in several sectors, including consumer electronics, construction, aerospace, defense, automotive, and marine industries, due to their strength and versatility.
Q3: What are the advantages of using extruded aluminum profiles?
A: They offer a combination of durability, lightweight nature, flexibility in design, and cost-effectiveness, making them ideal for numerous applications.
Q4: Can extruded aluminum profiles be customized?
A: Yes, they can be customized in terms of shape, size, and alloy composition to meet specific requirements of different projects and applications.
Q5: Are extruded aluminum profiles environmentally friendly?
A: Aluminum is recyclable and retains its properties post-recycling, making extruded aluminum profiles a sustainable choice in manufacturing and design.
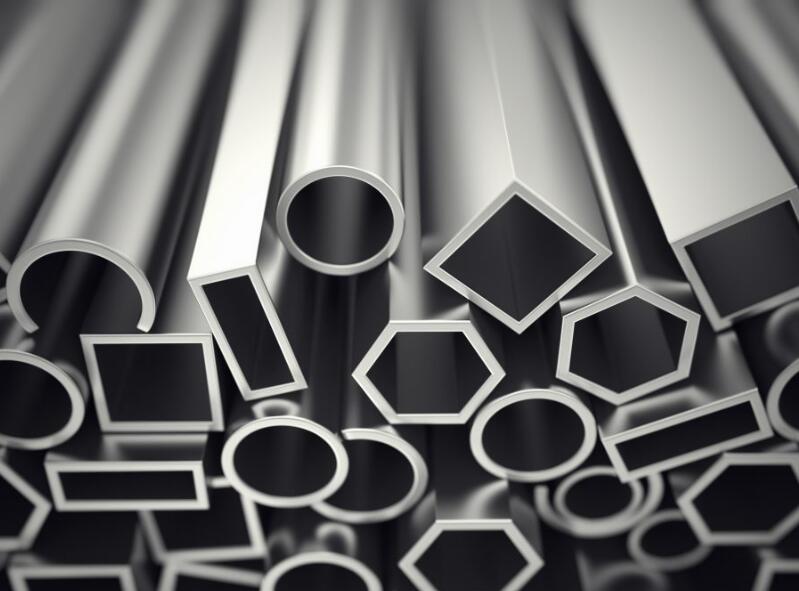