Introduction to Aluminum Formwork
Definition and Basic Understanding
Aluminum formwork represents a revolutionary development in the construction industry, particularly in the creation of concrete structures. Fundamentally, it comprises a system of panels and components crafted from high-strength aluminum alloys, designed to shape and support concrete until it hardens. Unlike traditional materials like wood or steel, aluminum formwork offers a unique combination of lightweight properties and robustness, making it an increasingly preferred choice for modern construction projects. Aluminum’s natural resistance to rust and corrosion further enhances its longevity, ensuring that it can be reused numerous times across different projects. This reusability not only makes it a cost-effective solution but also contributes to sustainable construction practices by reducing waste.
Historical Evolution and Modern Usage
The evolution of aluminum formwork can be traced back to its inception as a niche alternative to more traditional formwork materials. Over time, its adoption has grown significantly due to the increasing demand for efficient, sustainable, and cost-effective construction methods. In modern construction, aluminum formwork is extensively used in high-rise buildings, residential complexes, and even in intricate architectural designs. Its adaptability to various architectural layouts, coupled with the precision it brings to concrete structures, underscores its importance in the contemporary construction landscape. Notably, the system not only supports the concrete but also expedites other construction processes, such as the installation of mechanical and electrical conduits, thereby streamlining project timelines.
Overview of Different Aluminum Formwork Systems
There are several aluminum formwork systems available in the market, each designed to cater to specific construction needs. Systems like the Doka Monolithic and TECON Aluminium Formwork exemplify the diversity in design and functionality. The Doka Monolithic system is renowned for its optimized performance and functional versatility, particularly in facilitating the use of online shopping platforms for construction supplies. TECON’s Aluminum Formwork, on the other hand, includes various subsystems like Aluflex and Aludeck, which are engineered for lighter weight and increased reuse times. These systems exemplify how aluminum formwork has evolved to offer tailored solutions, accommodating everything from the walls and slabs to more complex structures like staircases, all while maintaining a focus on efficiency and ease of use.
Advantages of Using Aluminum Formwork
Lightweight and Easy Handling
One of the primary advantages of aluminum formwork is its lightweight nature, which significantly eases the burden of handling and transportation on construction sites. Unlike heavier alternatives like steel formwork, aluminum can be maneuvered manually, reducing the reliance on cranes and heavy lifting equipment. This not only accelerates the construction process but also enhances on-site safety by minimizing the risks associated with handling heavy materials. Additionally, the ease of assembling and disassembling aluminum formwork contributes to faster construction cycles, enabling projects to meet tight deadlines with greater efficiency. The physical properties of aluminum, particularly its strength-to-weight ratio, play a crucial role in its effectiveness, allowing it to support heavy loads while being easy to handle.
Increased Construction Efficiency
The use of aluminum formwork greatly amplifies construction efficiency, a crucial factor in modern building projects. Its ability to facilitate monolithic pouring — pouring walls and floors in a single operation — streamlines the construction process, yielding stronger structures and a superior concrete finish. This method not only reduces the time taken for concrete casting but also minimizes labor costs. The dimensional accuracy provided by aluminum formwork ensures uniformity in concrete structures, leading to a significant reduction in the need for corrective work post-construction. Furthermore, the system’s design allows for the quick removal and relocation of formwork, thereby enabling multiple uses in rapid succession. This aspect is particularly beneficial in large-scale projects where time and resource management are key.
Environmental Benefits and Reusability
Aluminum formwork stands out for its environmental benefits, primarily due to its high reusability factor. Unlike traditional materials that may only withstand a few uses before disposal, aluminum formwork can be reused hundreds of times without significant wear, thereby drastically reducing the waste generated in construction processes. This aspect not only makes it an environmentally responsible choice but also a cost-effective one in the long run, as the initial investment in aluminum formwork is offset by its extended lifespan and reduced maintenance needs. Moreover, aluminum is a recyclable material, adding another layer of environmental benefit. At the end of its lifecycle, aluminum formwork can be recycled, further minimizing its ecological footprint and contributing to sustainable construction practices.
Comparison: Aluminum vs. Steel Formwork
Weight and Strength Considerations
When comparing aluminum and steel formwork, the most evident distinction lies in their weight and strength. Aluminum, being significantly lighter than steel, offers ease of handling and mobility, making it ideal for projects where quick movement and assembly are required. Despite its lightweight nature, aluminum does not compromise on strength. It can withstand substantial pressure, making it suitable for various construction needs. Steel, while heavier and more labor-intensive to move, is known for its exceptional strength and durability. It is often used in projects where these properties are prioritized over ease of handling. This comparison highlights the importance of choosing the right formwork material based on specific project requirements and constraints.
Cost-Effectiveness and Lifecycle
Cost-effectiveness is a crucial factor in the choice between aluminum and steel formwork. Initially, aluminum formwork might appear more expensive due to its higher upfront cost. However, when considering its lifecycle, the investment in aluminum formwork becomes more economical. The ability to reuse aluminum formwork numerous times without significant degradation reduces the overall cost per use, making it a cost-effective solution in the long term. Steel formwork, while initially less expensive, may incur higher maintenance and replacement costs over time. The lifecycle cost analysis of both materials is essential for construction projects, particularly those with tight budgets and long-term sustainability goals.
Adaptability in Construction Projects
The adaptability of aluminum formwork in various construction projects is one of its most valued attributes. It can be tailored to fit a wide range of architectural designs and is particularly effective in high-rise building construction. Aluminum formwork’s flexibility allows it to accommodate different shapes and sizes, making it suitable for complex projects that require precise and intricate formwork. Steel formwork, while robust and durable, may not offer the same level of adaptability, especially in projects requiring intricate designs. Aluminum’s versatility extends to its ability to integrate with other construction activities, such as the installation of electrical and plumbing systems, further underscoring its suitability for diverse construction needs.
Implementing Aluminum Formwork in Construction
Key Components and Assembly
Implementing aluminum formwork in construction involves understanding its key components and assembly process. The system comprises various elements such as wall panels, beams, connectors, and braces, each playing a vital role in the formwork structure. Panels, the primary component, are designed for easy interlocking, facilitating quick assembly without specialized tools. Connectors and braces ensure stability and alignment of the formwork. The simplicity of assembling aluminum formwork significantly reduces the time and labor required, contributing to the efficiency of the construction process. Additionally, the uniformity and precision of these components ensure high-quality concrete finishes and structural integrity, making aluminum formwork a reliable choice for constructors.
Case Studies: Success Stories in Modern Construction
Case studies of aluminum formwork in modern construction highlight its effectiveness and versatility. For instance, projects like high-rise residential buildings have benefitted immensely from the use of aluminum formwork, achieving faster construction times and superior concrete finishes. The TECON Aluminium Formwork system, with its various subsystems, has been instrumental in such successes, demonstrating its adaptability to different project requirements. Another notable example is the Doka Monolithic system, known for its optimized performance in various construction scenarios. These case studies exemplify how aluminum formwork has transformed the construction industry, offering efficient and cost-effective solutions for complex and large-scale projects.
Future Trends and Technological Innovations
The future of aluminum formwork in construction is closely tied to technological innovations and evolving industry trends. With the increasing focus on sustainable and efficient construction practices, aluminum formwork is poised to play a significant role. Advancements in manufacturing technologies are expected to further enhance the efficiency, durability, and adaptability of aluminum formwork systems. Innovations such as integrating smart technology for precision and quality control are likely to emerge, aligning aluminum formwork with the digital transformation of the construction industry. These developments will not only improve the performance of aluminum formwork but also open up new possibilities for its application in various types of construction projects.
Challenges and Limitations
Initial Cost and Investment
While aluminum formwork offers numerous advantages, it is not without challenges, the most notable being the initial cost and investment. The upfront cost of aluminum formwork is higher compared to traditional materials like wood or steel. This initial investment can be a significant barrier for smaller construction projects or companies with limited budgets. However, it is important to consider the long-term savings offered by aluminum formwork, including reduced labor costs, shorter construction times, and lower maintenance expenses. For large-scale projects or those with a focus on sustainability and efficiency, the initial cost of aluminum formwork can be justified by its numerous benefits over its lifecycle.
Repair and Maintenance Issues
Another challenge associated with aluminum formwork is related to its repair and maintenance. While aluminum is durable and resistant to corrosion, it is not immune to wear and tear. Damages such as dents or deformations can occur, especially in high-use scenarios. Repairing aluminum formwork can be challenging and sometimes impossible, particularly if the damage is severe. This limitation necessitates careful handling and maintenance of the formwork to extend its usability. Regular inspections and adherence to proper usage guidelines are essential to prevent damage and ensure the longevity of the formwork.
Limitations in Design Flexibility
Aluminum formwork, despite its adaptability, faces limitations in design flexibility. While it is suitable for a wide range of construction projects, there are instances where its rigid structure may not conform to unique or unconventional architectural designs. This limitation can be a constraint in projects that require highly customized formwork solutions. However, advancements in manufacturing techniques and the development of modular formwork systems are addressing these limitations, offering more flexibility and customization options in aluminum formwork design.
Conclusion: The Future of Aluminum Formwork in Construction
Summarizing Key Takeaways
In conclusion, aluminum formwork has emerged as a game-changer in the construction industry, offering efficiency, cost-effectiveness, and environmental benefits. Its lightweight nature, ease of handling, and reusability make it a preferred choice for modern construction projects. While challenges such as initial cost and design limitations exist, the overall advantages of aluminum formwork make it a viable and promising solution for future construction endeavors.
Potential Developments and Industry Outlook
The potential for further developments in aluminum formwork is significant, with technological advancements and sustainability goals driving innovation. The integration of smart technologies and the development of more versatile formwork systems are likely to enhance its application and efficiency. As the construction industry continues to evolve, aluminum formwork is expected to play a pivotal role in shaping modern construction practices, aligning with the global trend towards sustainable and efficient building methods.
Final Thoughts and Recommendations
For construction professionals and companies considering aluminum formwork, it is recommended to evaluate the specific needs of their projects and weigh the long-term benefits against the initial investment. Embracing aluminum formwork can lead to significant improvements in construction efficiency, quality, and sustainability. As the industry moves forward, staying informed about the latest developments in formwork technology will be crucial for making informed decisions and staying competitive in the dynamic construction landscape.
FAQ Generation
Frequently Asked Questions
Q1: What is Aluminum Formwork?
A1: Aluminum formwork is a construction system for forming cast-in-place concrete structures of a building. Made from aluminum alloy, it’s known for its strength, lightweight, and high reusability rate, making it a preferred choice in modern construction for creating walls, floors, beams, and more.
Q2: How does Aluminum Formwork compare to Steel Formwork?
A2: Aluminum formwork is lighter than steel formwork, making it easier to handle and install. It’s also more adaptable to different architectural designs and is more cost-effective in the long run due to its reusability. Steel formwork, while strong and durable, is heavier and less flexible in terms of design adaptability.
Q3: What are the advantages of using Aluminum Formwork?
A3: The main advantages of aluminum formwork include its lightweight nature, ease of assembly, increased construction efficiency, environmental friendliness due to reusability, and the ability to achieve high-quality concrete finishes.
Q4: Are there any limitations to using Aluminum Formwork?
A4: The limitations of aluminum formwork include a higher initial investment cost, potential challenges in repairing damages, and some constraints in design flexibility for highly customized architectural designs.
Q5: What is the future outlook for Aluminum Formwork in construction?
A5: The future of aluminum formwork in construction is promising, with ongoing advancements in technology enhancing its efficiency, versatility, and sustainability. It’s expected to play a significant role in modern construction, aligning with global trends towards more efficient and eco-friendly building practices.
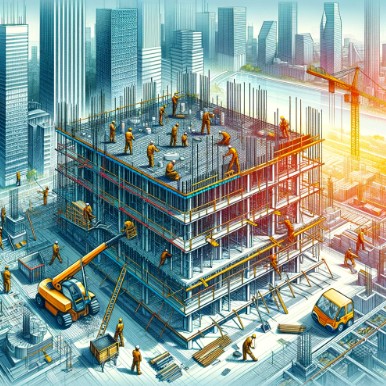