Introduction
In the realm of lighting, aluminum frames stand as silent guardians, protecting and enhancing the glow of lamp beads. Today, we embark on a journey through the production process of these vital components, shedding light on the craftsmanship behind every lamp.
Designing the Aluminum Frame
Crafting an aluminum frame begins with meticulous design considerations. Cross-sectional drawings are drafted with precision, balancing material efficiency with load-bearing capabilities. The aim is to create frames that not only safeguard lamp components but also facilitate seamless assembly.
Mold Preparation and Production
Before production commences, molds undergo rigorous preparation, including nitriding and testing. Only after qualifying can the mold be opened, signaling the initiation of the production process, where molten aluminum is carefully shaped into the desired frame profiles.
Processing and Treatment of Aluminum Profiles
Once formed, aluminum profiles undergo essential treatments to enhance their properties. Quenching and aging processes optimize the material’s strength and durability, while surface treatments ensure a pristine finish, ready to withstand the test of time.
Machining and Assembly
Customization is key in the world of aluminum frames. Some profiles require intricate machining, including punching, riveting, or CNC processing, tailored to the specific needs of each customer. Precise sawing at 45-degree angles facilitates seamless 90-degree connections, ensuring flawless assembly.
Packaging and Conclusion
As the final step in the production journey, aluminum frames are meticulously packaged for safe transport and storage. Whether pallet packaging or carton packaging, each frame is prepared with care, ready to illuminate spaces with brilliance and style.
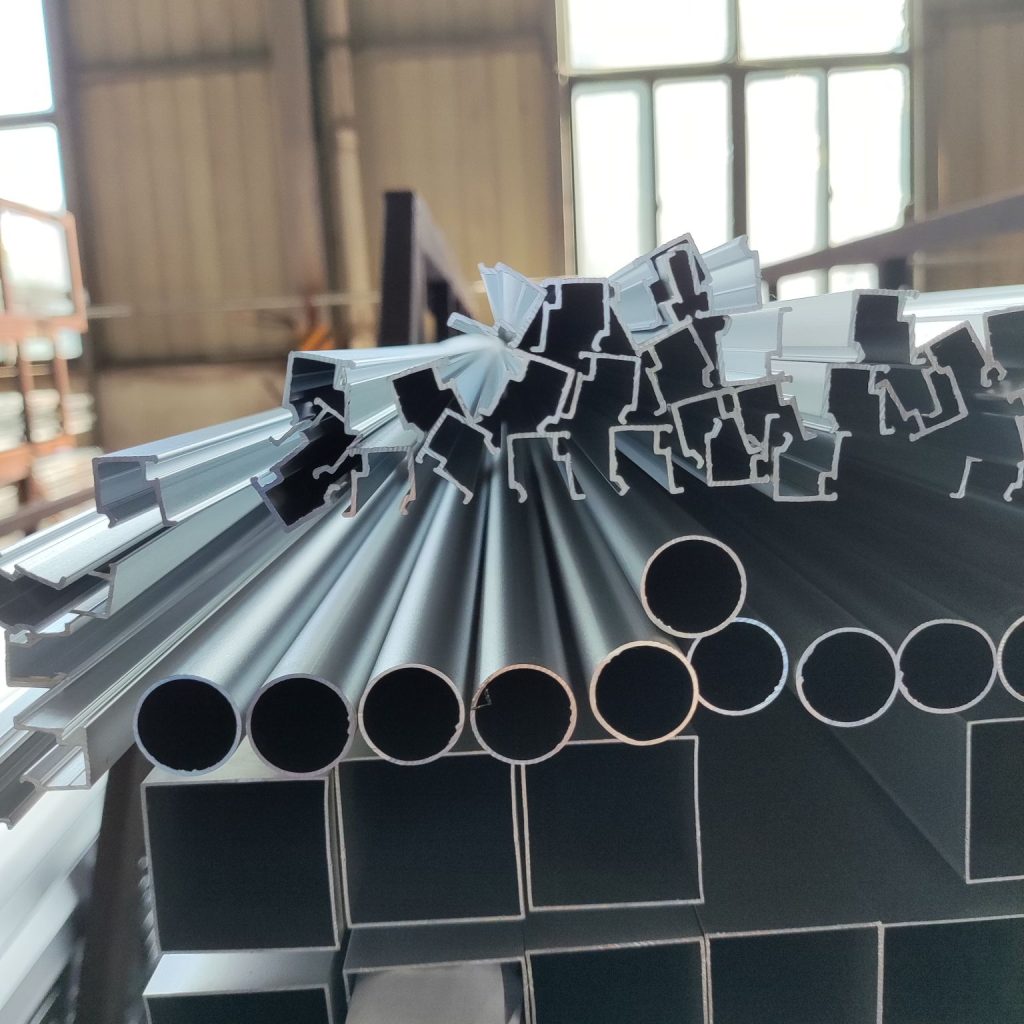