Follow Rina to show you more information about aluminum profiles
Hey there, aluminum enthusiasts! Rina Meng here, your go-to gal for all things aluminum profiles. Today, I want to dive into the fascinating world of industrial aluminum profile production process flow. Buckle up, because we’re about to embark on a wild and witty ride through the ins and outs of this aluminum extravaganza!
Let’s start at the beginning, shall we? The selection of raw materials is like picking the perfect ingredients for a scrumptious dish. Industrial aluminum profiles are made by heating aluminum rods and extruding them with a die, resulting in different cross-sectional shapes. But here’s the twist— the added alloys change the game, altering the mechanical properties and application fields of these profiles. It’s like adding a dash of spice to your favorite recipe, making it unique and oh-so-delicious!
Now, let’s talk about the production of aluminum rods. Trust me, it’s no piece of cake. We need to pay attention to various factors like the content of active impurities, alloy composition, melt superheat temperature, and even the speed of casting those 6063 aluminum rods. It’s a delicate dance of science and craftsmanship, my friends.
Once we have our aluminum rods ready, it’s time to heat things up! The heating treatment of these rods requires precise temperature control— we don’t want them to feel like they’re in a sauna or left out in the cold. We need that Goldilocks temperature, just right for extrusion and online quenching. It’s like finding the perfect temperature for your morning cup of joe— too hot, and it’ll scorch your taste buds; too cold, and it’s just a sad excuse for coffee.
Ah, molds! The unsung heroes of the industrial aluminum profile production process. These babies are designed with high-precision specifications to extrude profiles with the desired shapes and sizes. We must ensure that the structure meets production needs while adhering to the laws of physics and mechanics. And let’s not forget about the material selection and hardness of the mold— gotta avoid any deformities or scratches that might ruin the party. So, clean and inspect those molds regularly, my friends. We don’t want any uninvited guests like burrs or scratches spoiling our aluminum extravaganza!
Now, let’s get to the heart of the matter— industrial aluminum profile extrusion. Temperature control is the name of the game here. It’s like walking a tightrope, balancing the extrusion temperature to ensure top-notch product quality, production efficiency, mold longevity, and energy consumption. And hey, don’t forget about the extrusion speed! It’s a delicate dance that affects thermal effects, deformation uniformity, mechanical properties, and surface quality. We wouldn’t want our profiles to come out looking like a Picasso painting gone wrong, right?
Speaking of quenching, let’s dive into the marvelous world of on-machine quenching. We’re talking about rapid cooling those profiles to retain their strength. It’s like giving them a refreshing dip in a cool pool after a hot and sweaty workout. The cooling rate is crucial, and we can adjust it by changing fans and their rotation speeds. It’s all about finding that sweet spot and keeping our profiles cool as cucumbers.
Now, let’s straighten things out! After extrusion, industrial aluminum profiles might have a slight deviation. No worries, though. We have a trusty straightening machine to bring them back in line, within the required tolerance range. Straightening and correction are like giving those profiles a much-needed yoga session, ensuring they’re aligned and ready for action.
Ah, aging— it’s not just for fine wine and cheese! Aluminum profiles need aging too, to increase their strength. We have a meticulous production process in place to make sure everything goes smoothly. From ingot temperature control to online quenching processes, we’re all about dotting our i’s and crossing our t’s. And let’s not forget about the setting and control of aging furnace temperature— we need that sweet spot to achieve the perfect aging results. It’s like finding the ideal balance between a cozy fireplace and a hot summer day.
Blank framing and furnace loading might sound like a mundane task, but it’s crucial to ensure the quality of our industrial aluminum profiles. We can’t have them crowded together like sardines in a can— there needs to be some breathing room. And when it comes to combining different materials, like pipe materials and sheet materials, we need to think about airflow and circulation. It’s like arranging a party with the right mix of guests— give them some space to mingle, and the good vibes will flow!
Finally, we’ve reached the grand finale— packaging! Since industrial aluminum profiles are all about aesthetics and quality, we take packaging seriously. We’re talking about affixing a film on the surface to avoid any scratches, wrapping them in pearl cotton for that extra touch of elegance, and adding a layer of kraft paper to protect them from those pesky hard objects. It’s like dressing up our profiles for a fancy soirée— they deserve to make a grand entrance wherever they go!
Overall, the industrial aluminum profile production process flow is a thrilling journey filled with challenges and triumphs. It’s a delicate balance of science, art, and a touch of magic. And hey, I hope this little adventure through the world of aluminum profiles brought a smile to your face and a twinkle to your eye. Remember, aluminum is the unsung hero in our everyday lives— it’s strong, lightweight, and endlessly versatile. So, let’s raise a toast to the incredible world of industrial aluminum profiles!
Thanks for joining me on this aluminum extravaganza, folks! Until next time, stay aluminum-awesome and keep shining bright like a diamond. Catch you on the flip side, my fellow aluminum enthusiasts!
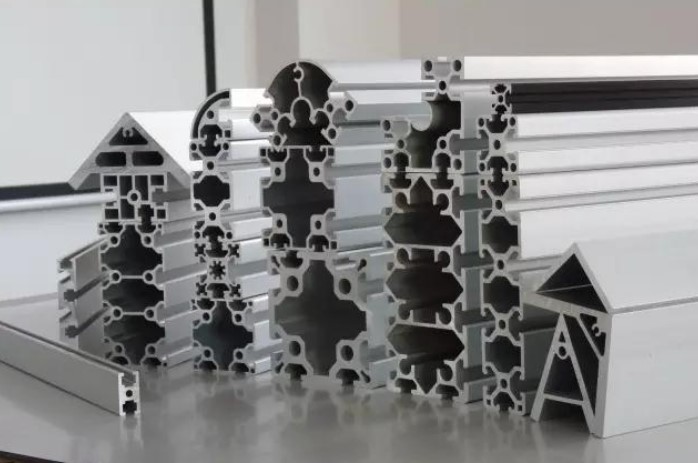