Introduction
Aluminum alloys stand as crucial materials across industries, prized for their lightweight, durability, and corrosion resistance. However, to fully leverage these properties, proper surface treatment is essential. This comprehensive guide explores various surface treatment methods tailored for aluminum alloys, enhancing their performance and extending their lifespan.
Sandblasting: Enhancing Surface Preparation
Sandblasting serves as a foundational step, effectively cleaning aluminum surfaces and improving adhesion for subsequent treatments. While beneficial, its efficacy is surpassed by chemical coating pretreatments, which offer superior outcomes in many applications.
Coloring Processes: Adding Aesthetic and Functional Value
Aluminum oxidation and electrophoresis coloring processes introduce vibrant colors to oxide films, meeting diverse industrial needs—from sleek black finishes for optical instruments to radiant golden hues for commemorative badges.
Conductive Oxidation: Balancing Protection and Conductivity
Ideal for applications demanding both protection and conductivity, conductive oxidation (chromate conversion film) offers a viable solution, albeit with specific limitations compared to alternative treatments.
Chemical Oxidation: Versatility in Film Formation
Distinguished by solution properties (alkaline vs. acidic), chemical oxidation yields oxide, phosphate, chromate, and chromic acid-phosphate films. Each variant finds application across industries, contributing varying levels of wear and corrosion resistance.
Electrochemical Oxidation: Strengthening Aluminum’s Armor
Electrochemical oxidation impresses with its ability to produce thick oxide films boasting high hardness, heat resistance, and superior corrosion resistance. This method proves versatile and efficient across diverse aluminum applications.
Spraying: Protecting and Decorating Aluminum
Used primarily for external protection and aesthetic enhancement, spraying builds upon oxidation bases. Effective pre-treatment methods like phosphating and chromating ensure durable adhesion between coatings and aluminum substrates.
Chemical Polishing: Smoothing Aluminum Surfaces
Through selective self-dissolution in electrolyte solutions, chemical polishing levels aluminum surfaces, reducing roughness and enhancing aesthetic appeal. Its efficiency and cost-effectiveness make it a preferred choice in many manufacturing scenarios.
Passivation: Safeguarding Against Corrosion
Transforming aluminum surfaces into a corrosion-resistant state, passivation forms a protective film that significantly enhances longevity and durability, crucial in environments prone to oxidation.
Conclusion
Selecting the right surface treatment method for aluminum alloys hinges on understanding specific application requirements. Whether enhancing aesthetics, improving conductivity, or fortifying against corrosion, each method discussed offers unique advantages tailored to meet diverse industrial needs.
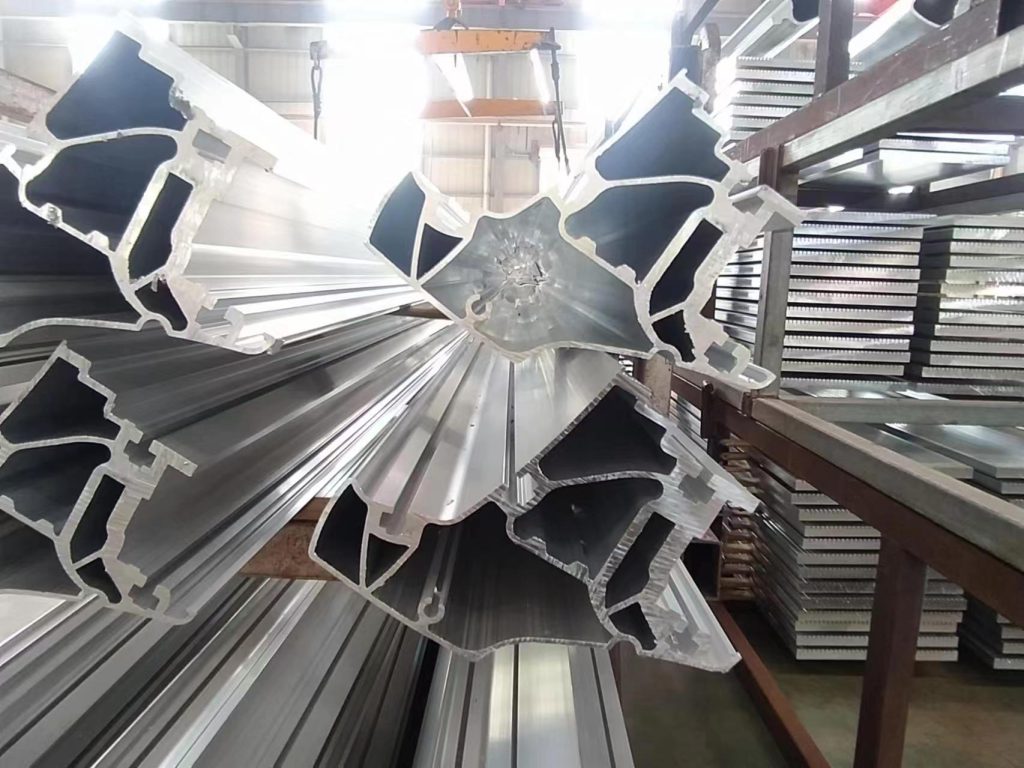