Introduction
Industrial aluminum profiles, the backbone of countless manufacturing projects, stand out for their versatility and strength. Before these profiles can fulfill their roles in various applications, they undergo a series of processing steps to meet specific project requirements. This article delves into the essential processing techniques that transform raw aluminum profiles into precision components for industrial use.
The Fundamentals of Industrial Aluminum Profile Processing
At their core, industrial aluminum profiles are semi-finished products shaped through the extrusion of aluminum ingots. The transformation from a standard extrusion to a component ready for industrial application hinges on several key processing methods. Understanding these techniques is crucial for anyone looking to leverage aluminum profiles in their projects.
Processing Techniques for Industrial Aluminum Profiles
- Cutting Cutting is the first step in aluminum profile processing, tailoring lengths and angles to specific project needs. This customization ensures that each piece fits its intended purpose perfectly, whether it’s forming part of a machine frame or a structural component.
- Drilling Holes Drilling, or turning holes, introduces installation and process holes into the profile surface. These holes are essential for attaching accessories with bolts and nuts, facilitating seamless assembly and connection of components.
- Tapping Tapping introduces threads into drilled holes, allowing bolts to be screwed directly into the profile. This technique eliminates the need for nuts, streamlining the assembly process and enhancing structural integrity.
- Finishing Finishing, often performed with CNC equipment, includes various milling processes that refine the profile’s features. This step is critical for ensuring that each component meets precise specifications and integrates smoothly into larger assemblies.
- Assembly For clients without the capability to assemble profiles, companies offer complete assembly services. This includes everything from delivery and on-site measurement to the installation of processed profiles, ensuring a turnkey solution for complex projects.
Importance of Precision and Quality in Processing
The quality of the final aluminum profile product heavily depends on the precision of each processing step. Even minor errors can compromise the functionality and aesthetics of the component, highlighting the need for expert handling and advanced equipment.
Customization and Application Solutions
Experienced providers like Anhui Shengxin Aluminum Co., Ltd., with over 20 years in the industry, offer customized processing services that cater to specific project requirements. Their expertise ensures that each profile is processed with the utmost precision, ready to fulfill its role in diverse industrial applications.
Conclusion
The processing of industrial aluminum profiles is a nuanced art that requires detailed knowledge and specialized equipment. From cutting to assembly, each technique plays a pivotal role in preparing aluminum profiles for their essential functions in various industries. As we’ve explored, entrusting this process to experienced professionals guarantees the high-quality results essential for success in today’s competitive market.
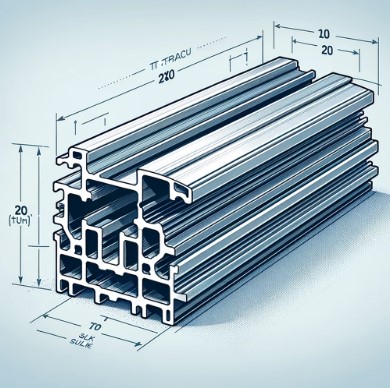