Introduction
Aluminum hard oxidation coloring is a critical process in surface finishing, requiring meticulous attention to detail to achieve uniform and stable coloration. To minimize the risk of coloring defects and ensure high-quality results, adhering to key operational requirements is paramount. In this article, we delve into the essential guidelines for effective aluminum hard oxidation coloring and their significance in achieving optimal outcomes.
Key Operational Requirements for Aluminum Hard Oxidation Coloring
Proper Handling and Placement: Ensuring the profile’s correct inclination and placement in the coloring tank to maintain uniform coloring and prevent unevenness.
Checking Bath Liquid Concentration: Regularly verifying the concentration of the aluminum hard oxidation bath liquid to meet process requirements and avoid color discrepancies.
Preparing for Coloring Power Supply: Disengaging hooks and allowing a brief standstill period before supplying power for coloring to ensure optimal conditions.
Ensuring Equal Coloring Voltage: Adjusting power supply voltage in advance to maintain consistent coloring voltage for uniform coloration.
Prompt Removal and Washing: Immediately lifting profiles after coloring to drain tank liquid promptly and transfer for thorough washing to prevent residual contamination.
Timely Adjustment of Coloring Time: Controlling coloring time to avoid over-coloring, particularly for sensitive colors like gold.
Secondary Water Washing: Conducting secondary water washing before further treatment to remove residual pigments and maintain coloring integrity.
Importance of Pre-Dye Washing: Strengthening washing before dyeing to eliminate residual acid and alkali that may affect the dyeing process and surface quality.
Immediate Dyeing After Anodization: Dyeing profiles promptly after anodization to prevent pore shrinkage and dirt accumulation, ensuring optimal dye penetration.
Preventing Overlapping During Dyeing: Ensuring profiles do not overlap during dyeing to prevent uneven coloring and surface irregularities.
Thorough Rinsing After Dyeing: Conducting thorough rinsing after dyeing to remove any residual pigments and maintain the integrity of the hard oxidation layer.
Significance of Adhering to Operational Requirements
Effective adherence to operational requirements is crucial for achieving consistent, high-quality results in aluminum hard oxidation coloring. By following these guidelines, manufacturers can minimize the risk of defects, ensure uniform coloration, and enhance overall product quality and stability.
Practical Tips for Effective Aluminum Hard Oxidation Coloring
In addition to adhering to operational requirements, implementing practical tips such as proper training, regular maintenance, and continuous monitoring can further optimize aluminum hard oxidation coloring processes, ensuring consistent and reliable outcomes.
Conclusion
Mastering aluminum hard oxidation coloring requires strict adherence to operational requirements and continuous quality control measures. By prioritizing proper handling, meticulous preparation, and thorough post-processing, manufacturers can achieve superior coloration results, minimize defects, and enhance the overall quality and stability of aluminum products.
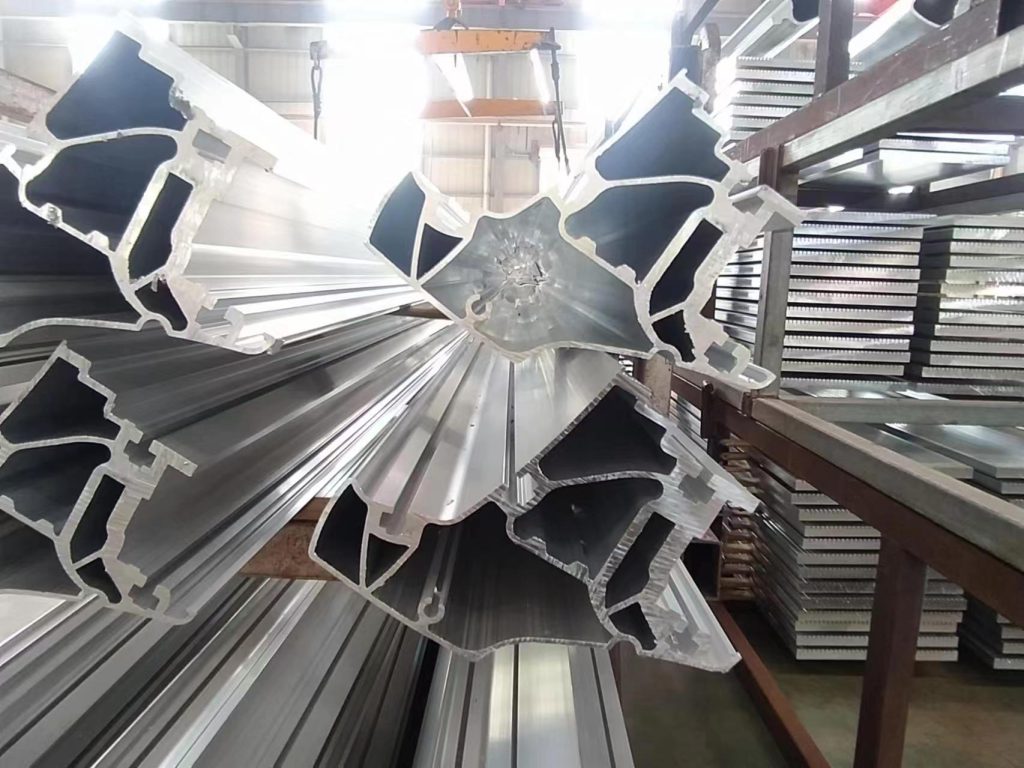