Introduction
In today’s rapidly evolving industrial landscape, aluminum profiles have emerged as indispensable materials, finding extensive applications in aerospace, automotive manufacturing, construction, and more. Among the various types of aluminum profiles, rectangular cross-section profiles stand out for their structural stability and excellent mechanical properties. However, to meet specific design requirements, these profiles often undergo press bending, a complex forming process that warrants thorough investigation and understanding.
Basic Principles of Press Bending
Press bending involves subjecting aluminum profiles to external pressure or impact forces, causing them to deform plastically. This process relies on bending moments to induce stress and strain within the material, thereby altering its shape. Various factors such as material properties, cross-sectional shape, and bending radius influence the effectiveness of press bending, necessitating careful consideration during the process.
Bending Characteristics of Rectangular Cross-section Aluminum Profiles
Rectangular aluminum profiles present unique challenges during the bending process, including cross-sectional distortion and wall thickness reduction. Achieving optimal forming quality requires meticulous attention to factors such as material plasticity, mold precision, and control of bending forces. By addressing these challenges, manufacturers can ensure the accuracy and integrity of the formed profiles.
Optimization of Press Bending Process Parameters
To attain high-quality press bending results, it’s essential to optimize process parameters such as bending speed, force, and mold design. These parameters significantly impact the deformation process, influencing outcomes such as distortion reduction and thickness uniformity. Through systematic parameter adjustments, manufacturers can enhance forming stability and accuracy, paving the way for superior aluminum profile products.
Future Prospects and Conclusion
Research on press bending for rectangular aluminum profiles remains a vital area of exploration. By continuously refining process parameters and advancing mold design techniques, manufacturers can elevate the quality and applicability of aluminum profiles across diverse industries. As technology evolves and new materials emerge, further breakthroughs in profile forming processes are anticipated, driving innovation and progress in the field.
In summary, mastering the press bending process for rectangular aluminum profiles is essential for meeting the demands of modern industrial applications. By understanding the principles, addressing challenges, and embracing optimization strategies, manufacturers can unlock new possibilities and propel the evolution of aluminum profile technology.
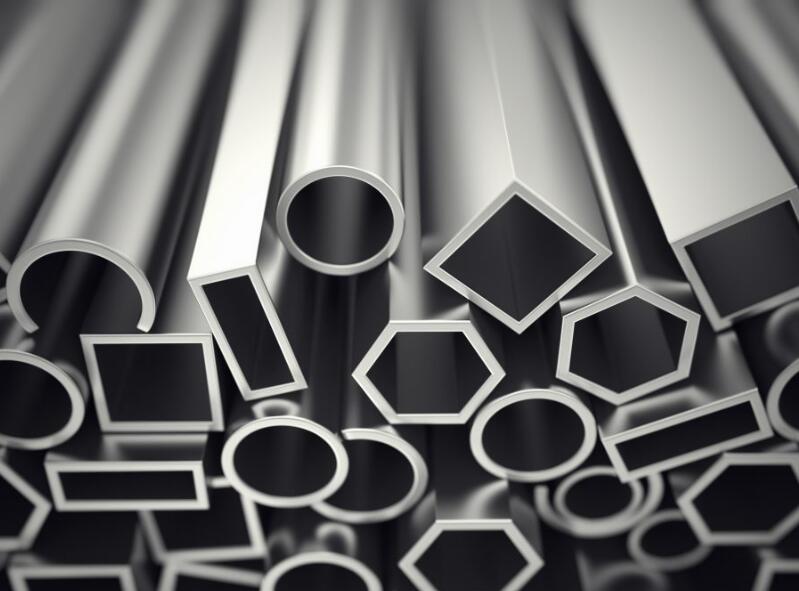