Introduction
In the vast world of industrial metals, aluminum stands out for its combination of lightness and strength. Yet, the journey from raw aluminum to a finished industrial product isn’t straightforward. Post-production treatments, such as oxidation, are essential for enhancing the metal’s surface hardness and corrosion resistance, thereby ensuring its longevity in various applications. This article delves into the oxidation process and subsequent treatments that industrial aluminum undergoes to meet stringent quality standards.
Understanding the Oxidation Process
Oxidation, in the context of industrial aluminum, involves an electrolytic process where the aluminum acts as the anode. This process induces the formation of a dense, artificial oxide film on the surface. Not only is this film transparent and tough, but it also considerably extends the material’s usable life by protecting against corrosion and wear.
Post-Oxidation Treatments for Aluminum
After oxidation, aluminum isn’t quite ready for the market. It undergoes several post-treatment processes to ensure the quality of the oxide layer. These commonly include sulfuric acid anodizing, the most frequently used method due to its effectiveness and cost-efficiency.
Hot water washing then follows, where control over water temperature and washing duration is crucial. Overdoing either can thin the oxide layer and alter any coloration applied. The drying process succeeds washing, with the aluminum hung in a way that allows natural water flow-off, preserving the oxide layer’s sheen. Depending on the climate, aging the aluminum can be done under the sun or in an oven, setting the oxide layer’s qualities firmly in place.
Specialized Anodizing Techniques
Oxalic acid anodizing presents an alternative with certain benefits over the conventional sulfuric method. Its lower solubility in the oxide film means better wear resistance and electrical insulation. However, it comes with higher costs and variable color outcomes, limiting its applications. The stability of the electrolyte during oxalic acid anodization is another concern, often leading to process-related color inconsistencies.
Conclusion
Through oxidation and meticulous post-treatment processes, industrial aluminum achieves a state fit for demanding applications. These treatments not only improve the metal’s durability but also its aesthetic appeal—crucial for end-users across various industries. As technology advances, so too will these processes, ensuring aluminum remains a versatile and reliable material in the industrial world.
By understanding the importance of these treatments and their impact on aluminum’s performance, stakeholders in the aluminum industry can appreciate the value they add to the final product—whether it’s in construction, transportation, or electronics.
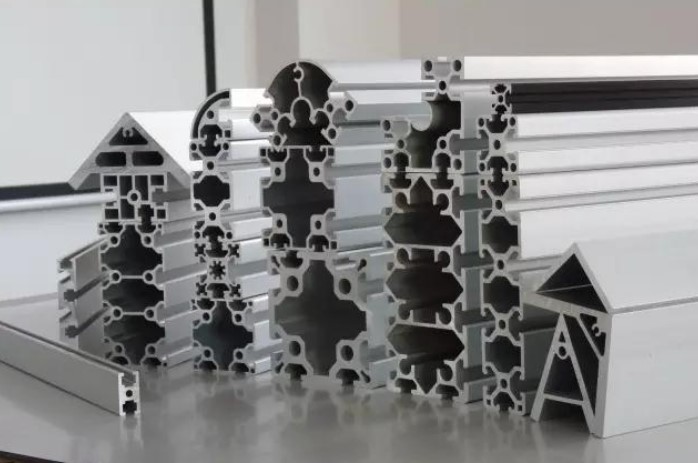