The Art and Science of Curved Aluminium Profiles
Introduction to Curved Aluminium Profiles
Curved aluminium profiles have become a cornerstone in modern architectural and industrial design, offering both aesthetic elegance and structural integrity. The process of curving large structural aluminium profiles, particularly for applications like curtain walls, requires not only advanced technology but also skilled operators. This intricate process ensures that the profiles are free from imperfections such as rippling or distortion, which could affect their connection with other components. The complexity lies in maintaining the precision and quality of the curve, especially in large profiles, as seen in Alubend’s work with 225mm wide structural profiles curved to a 1560mm inside radius. This introduction sets the stage to explore the various applications, manufacturing techniques, and quality standards that define the world of curved aluminium profiles.
Applications of Curved Aluminium Profiles
Curved aluminium profiles find diverse applications in architecture and consumer products. In architectural settings, they are used for creating innovative curtain wall structures, window shading systems, and solar shading solutions. These applications not only enhance the aesthetic value of buildings but also contribute to their functional efficiency. In the consumer sector, curved aluminium profiles are integral to products like lighting solutions, prams, and caravans. The ability to integrate these profiles into various designs allows for greater freedom and creativity in both industrial and consumer product development. This versatility highlights the material’s adaptability and its role in pushing the boundaries of design and functionality.
Manufacturing Process and Techniques
The manufacturing of curved aluminium profiles involves several critical considerations, particularly concerning the alloy’s properties and the desired outcome. Alloys from the 6xxx-series are often chosen for their balance between strength and deformability. However, profiles with higher strength, like those made from EN AW-6082, present greater challenges in forming. The heat treatment process also plays a crucial role, typically involving bending in the T4 condition and aging to T6 afterwards. The choice of bending process, whether it be roll bending, stretch bending, or mandrel bending, depends on the profile’s application and production volume. Each method has its own merits, tailored to the specific requirements of the profile’s design and intended use.
Quality Assurance and Standards in Curving Aluminium
Quality assurance is paramount in the curving of aluminium profiles. Manufacturers like Alubend employ various checks to ensure the highest standard of quality. These include flatness checks on granite tables, visual inspections under high brightness LED light, CMM dimensional scanning, and the use of go/no go jigs and full-size printed plots. Special attention is required when bending sections with thermal breaks due to the significant strength difference between aluminium and the thermal material. Such precision in quality control underlines the complexity and technical sophistication involved in producing curved aluminium profiles that meet both aesthetic and structural standards.
Innovations and Advances in Aluminium Profile Curving
The field of curved aluminium profiles is marked by continuous innovation and technological advancements. Manufacturers are constantly exploring new methods and technologies to enhance the efficiency and precision of the curving process. For instance, Alubend’s approach to curving large structural sections involves finite element analysis to determine the optimal force for each element of the profile. Such advancements not only improve the quality of the final product but also expand the possibilities for their application in various fields. These innovations reflect the ongoing evolution of aluminium curving techniques and their impact on modern design and architecture.
Conclusion
In conclusion, curved aluminium profiles represent a fascinating blend of art and science, combining aesthetic appeal with structural functionality. The process of creating these profiles involves a complex interplay of material properties, manufacturing techniques, and quality standards. As we have seen, innovations in this field are continuously pushing the boundaries, offering new possibilities in architectural and industrial design. The future of curved aluminium profiles looks promising, with potential advancements poised to further revolutionize their application and aesthetics.
FAQ Generation
Frequently Asked Questions
Q1: What are the primary applications of curved aluminium profiles?
A1: Curved aluminium profiles are widely used in architecture for curtain walls, window shading, and solar shading, as well as in consumer products like lighting solutions, prams, and caravans.
Q2: What factors are important in the manufacturing process of curved aluminium profiles?
A2: Key factors in manufacturing curved aluminium profiles include the choice of alloy, heat treatment process, and the bending technique, such as roll bending, stretch bending, or mandrel bending.
Q3: How is quality assurance maintained in curving aluminium profiles?
A3: Quality assurance involves multiple checks like flatness tests, visual inspections, dimensional scanning, and the use of specific tooling, especially when bending sections with thermal breaks.
Q4: What innovations are being made in the field of curved aluminium profiles?
A4: Innovations include new bending techniques, finite element analysis for precision curving, and advanced manufacturing processes to enhance the quality and application of curved aluminium profiles.
Q5: Why are curved aluminium profiles significant in modern design?
A5: Curved aluminium profiles offer aesthetic appeal and structural functionality, allowing for greater design freedom and innovation in both architectural and industrial applications.
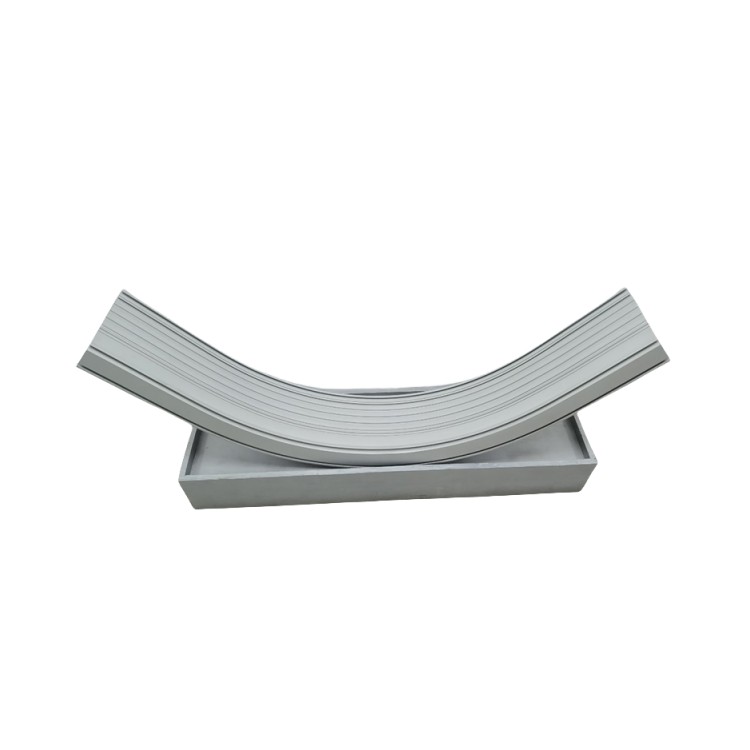