Aluminum alloys hold a vital position in the aerospace industry, primarily due to their ideal physical and mechanical properties. These alloys offer high strength, light weight, good corrosion resistance, and excellent processing performance, making them perfect for manufacturing aircraft, rockets, satellites, and other aerospace vehicles.
Key Properties of Aluminum Alloys
Aluminum alloys are highly valued in the aerospace field for several reasons:
High Strength and Light Weight: These alloys provide the necessary strength without adding excessive weight, crucial for aerospace applications.
Corrosion Resistance: Aluminum alloys resist corrosion, extending the lifespan and reliability of aerospace components.
Excellent Processing Performance: They are easy to work with, making them suitable for various manufacturing processes.
Commonly Used Aluminum Alloys in Aerospace
Two series of aluminum alloys are predominantly used in the aerospace industry: the 2000 series and the 7000 series.
2000 Series Aluminum Alloys: These alloys contain copper and magnesium, giving them good strength, toughness, and corrosion resistance. They are typically used for aircraft structural parts like wings and fuselages.
7000 Series Aluminum Alloys: Rich in zinc, these alloys offer higher strength and hardness, making them ideal for parts that endure high stress, such as landing gear and certain engine components.
Innovations and New Aluminum Alloy Materials
Researchers continually seek to improve and optimize aluminum alloys to meet the unique needs of aerospace applications. New production processes, such as powder metallurgy and injection molding, are being explored to create lightweight aluminum alloy materials with enhanced performance. Additionally, aluminum-based composites and superplastic aluminum alloys are emerging as hot topics in current research, promising higher specific strength and better corrosion resistance.
Specific Aluminum Alloys for Different Aerospace Applications
The aerospace field requires precise material selection based on the performance requirements of different parts. Commonly used aluminum alloy grades include 2X24, 7X75, and 7X5X, each with distinct chemical compositions and mechanical properties.
2X24 Aluminum Alloy: Known for its high strength, corrosion resistance, and good processing and welding properties, it is mainly used for structural parts such as wings, fuselages, and tails.
7X75 Aluminum Alloy: This high-strength, high-toughness alloy is resistant to fatigue and corrosion, making it suitable for critical load-bearing parts like landing gear and engine components.
7X5X Aluminum Alloy: With similar high strength and toughness, it is used for both structural and load-bearing parts, including wings and landing gears.
In the context of launch vehicles and manned spacecraft, specific aluminum alloys such as 7075, 20X4, and 2219 are used for different parts due to their unique properties. For example, 7075 is used in engine devices and main body parts for its high strength and corrosion resistance, while 2219 is preferred for liquid oxygen tanks due to its low-temperature performance and corrosion resistance.
Future Prospects and Advancements
The application prospects of aluminum alloys in aerospace are broad and promising. With continuous advancements in science and technology, we can anticipate the development of new aluminum alloy materials with superior performance. These advancements will further enhance the performance and safety of aerospace vehicles, contributing significantly to the industry’s growth.
Conclusion
Aluminum alloys play a crucial role in the aerospace industry due to their exceptional properties and wide range of applications. The continuous improvement and development of new aluminum alloy materials promise a bright future for aerospace technology. As we advance, these innovations will undoubtedly make greater contributions to the development and safety of aerospace vehicles.
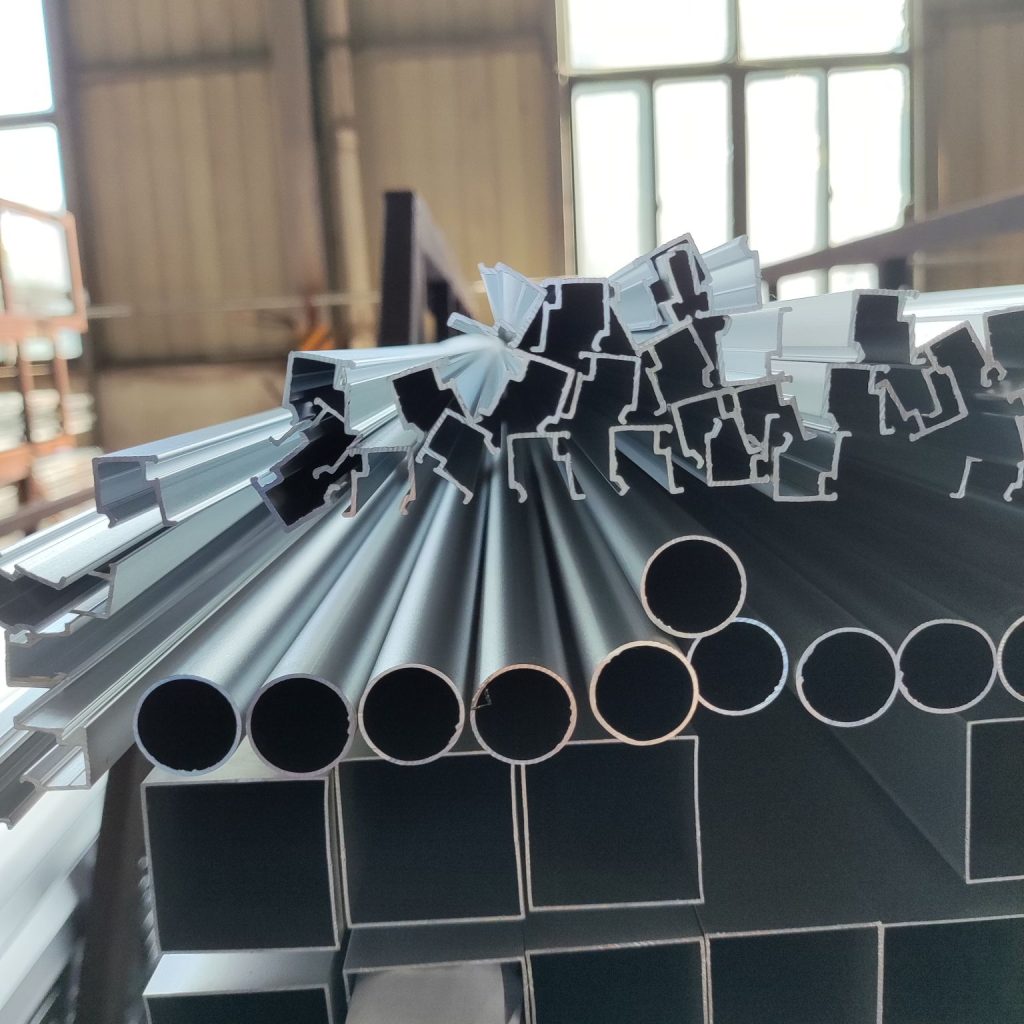