Follow Rina to show you more information about aluminum profiles
Hey there, fellow aluminum enthusiasts! Rina Meng here, ready to dive into the fascinating world of aluminum profiles. Today, we’re going to unravel the mystery behind the weight deviation of these shiny wonders. So, grab your thinking caps and let’s embark on this weighty adventure together!
Introduction: Settling the Aluminum Weight Debate
Okay, folks, let’s settle the score on how we determine the weight of aluminum profiles. There are two methods in the ring: weighing settlement and theoretical settlement. In the weighing settlement, we weigh the actual aluminum profile products, including the packaging, and calculate the payment based on the actual weight multiplied by the price per ton. On the other hand, the theoretical settlement involves multiplying the theoretical weight of the profile by the price per ton. Two methods, two outcomes—let the weight debate begin!
Step 1: Wall Thickness Deviation Dance
Ah, the wall thickness deviation—quite the weighty matter, my friends! You see, there’s a difference between the actual wall thickness and the theoretical wall thickness of the profile. And guess what? That difference leads to a discrepancy between the weighed weight and the theoretical weight. It’s like a tug of war between reality and theory!
Now, let’s crunch some numbers, shall we? According to the national standard GB/T5237.1, when the wall thickness of a window frame profile with a nominal thickness of 1.4mm deviates positively by 0.13mm, the weight difference per meter is around 0.055kg. Multiply that by the length of one ton of material, and we’re looking at a difference of 53kg. Whoa, that’s a whole lot of aluminum weight going astray!
But fear not, my friends! We have some tricks up our sleeves to control this deviation. It all starts with the quality of the aluminum profile mold. We need to ensure precision during the mold processing, keeping the wall thickness within a range of 0.05mm. And hey, let’s not forget about the production process. We control the extrusion speed and schedule regular maintenance for the molds. It’s like a well-choreographed dance, ensuring the wall thickness stays in check!
Step 2: Theoretical Weight Wonders
Hold on tight, because we’re about to dive into the realm of theoretical weight wonders! Different customers have different requirements for product wall thickness, and that affects the theoretical weight. Some customers only allow positive deviations, while others only allow negative deviations. It’s like a weight preference party, folks!
For example, let’s take a window mullion product with a wall thickness of 1.4mm. If the positive deviation is 0.26mm and the negative deviation is 0mm, the theoretical meter weight calculation gets interesting. When the wall thickness deviates positively, the meter weight increases to 1.309kg/m. On the flip side, when the wall thickness deviates negatively, the meter weight decreases to 1.192kg/m. It’s like a seesaw of weight fluctuations, my friends!
Now, let’s talk about the impact of these deviations. For a wall thickness of 1.4mm, the difference between the weighing weight and the theoretical weight ranges from 7% to 9% when the entire wall thickness increases or decreases. It’s like a weight rollercoaster ride, keeping us on our toes!
Step 3: Surface Treatment Layer Secrets
Ah, the surface treatment layer—the icing on the aluminum profile cake! Different surface treatments, such as oxidation, electrophoresis, spraying, and fluorocarbon, add their own weighty twist to the profiles.
When it comes to oxidation and electrophoretic profiles, the weight increase due to the surface treatment is minimal. We don’t lose much weight during the pretreatment process, balancing out the weight gain from the treatment. It’s like a delicate equilibrium, my friends!
Now, let’s talk about sprayed profiles. A layer of powder sprayed coating adds some weight to the profile, with the thickness ranging from 40μm to 120μm. And hey, don’t forget about the fluorocarbon paint sprayed profiles! The average coating thickness is not less than 30μm for two coats and not less than 65μm for four coats. It’s like adding a coat of armor to our profiles, making them stand out from the crowd!
Step 4: Packaging Puzzles
Ah, packaging—the final piece of the weight deviation puzzle! Different packaging methods, such as paper packaging and shrink film packaging, play a role in the overall weight of the profiles.
When it comes to paper packaging, there’s a limit to the weight of the paper. We aim to keep it below 6% of the total weight. That means the weight of the paper in one ton of profiles should not exceed 60kg. It’s like finding the perfect balance between protection and practicality!
And let’s not forget about shrink film packaging. The weight increase due to shrink film packaging is generally around 4%. We want to keep the weight of one ton of profile shrink film below 40kg. It’s like giving our profiles a snug and secure packaging, ready to embark on their journey!
Overall Reflection: Balancing the Weighty Equation
Phew, what a weighty adventure it has been, my friends! We’ve explored the deviations caused by wall thickness, the wonders of theoretical weight, the secrets of the surface treatment layer, and the puzzles of packaging. It’s like unraveling a complex equation, striving for that perfect balance.
As manufacturers, our goal is to control the difference between the weighed weight and the theoretical weight within 5%. We dance with molds, fine-tune production processes, and pay attention to every weighty detail. It’s like conducting a symphony of precision and control!
So, my fellow aluminum enthusiasts, let’s embrace the weight deviation quirks and strive for excellence. Remember, it’s all about finding that delicate balance and delivering top-notch aluminum profiles to the world!
Thank you for joining me on this weighty journey. Keep exploring, keep pushing boundaries, and may your aluminum endeavors be filled with success and a dash of humor!
Stay weighty and witty, and catch you on the flip side!
Catchphrase: Balancing the weighty equation, one aluminum profile at a time!
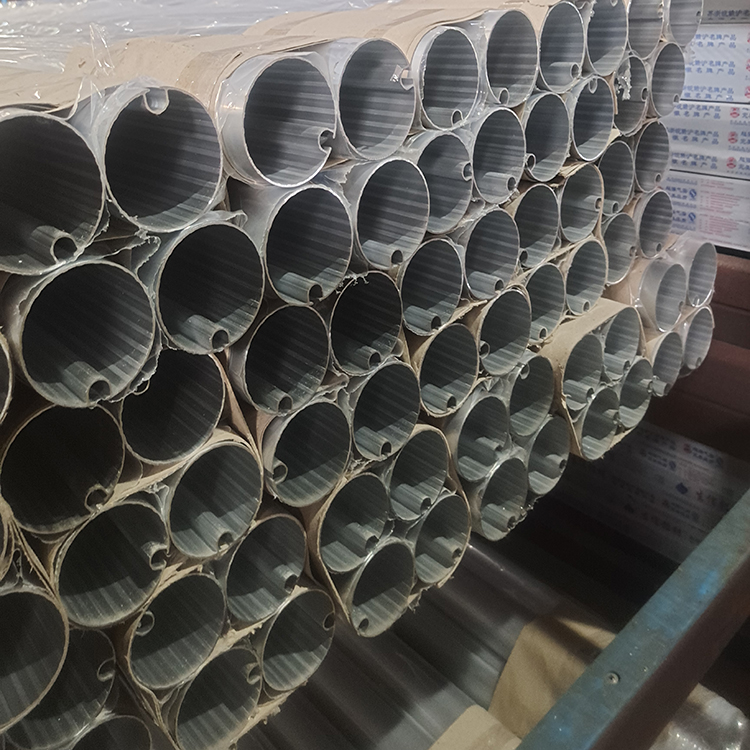