Aluminum alloys play a crucial role in modern industries, offering a blend of strength, durability, and versatility. Among them, the 6061 aluminum alloy stands out for its widespread use and distinctive properties, notably in its T6 and T651 states. In this article, we delve into the characteristics, differences, and applications of 6061T6 and 6061T651 aluminum alloys, helping you understand how to leverage their unique features for optimal performance.
Overview of 6061 Aluminum Alloy
6061 is an internationally recognized aluminum-magnesium-silicon alloy known for its excellent welding capabilities, superior anodizing effect, high strength, and resistance to corrosion. Available in various states including T6 and T651, it finds applications across diverse industries such as aerospace, automotive, marine, and structural components.
Difference Between 6061T6 and 6061T651
The distinction between 6061T6 and 6061T651 lies primarily in their processing treatments. 6061T6 undergoes heat treatment (quenching) to achieve specified hardness and strength levels but retains internal stresses that can cause deformation during subsequent processing. In contrast, 6061T651 involves additional steps like pre-stretching (artificial aging) to eliminate internal stresses, enhancing dimensional stability and reducing the risk of deformation.
Production Processes of 6061 Aluminum
6061 aluminum can be produced through rolling or extrusion methods, each tailored to specific end-product requirements. Rolling yields aluminum plates with precise thickness and uniform properties, while extrusion allows for the creation of custom profiles suited to diverse industrial applications.
Overcoming Deformation Challenges with 6061T6
Minimizing deformation in 6061T6 requires careful consideration of part size, processing allowances, and sequential machining techniques. By gradually releasing internal stresses through optimized processing steps, manufacturers can ensure product integrity and dimensional accuracy.
Cost-effectiveness Considerations
While 6061T6 may offer lower raw material costs compared to 6061T651, factors such as processing efficiency, tooling requirements, and overall production yield influence its cost-effectiveness in practical applications. Choosing between the two alloys depends on specific project needs and desired performance outcomes.
Conclusion
In conclusion, understanding the nuances between 6061T6 and 6061T651 aluminum alloys is essential for selecting the right material for your industrial or structural applications. Whether prioritizing strength, machinability, or dimensional stability, these alloys offer versatile solutions to meet diverse engineering challenges.
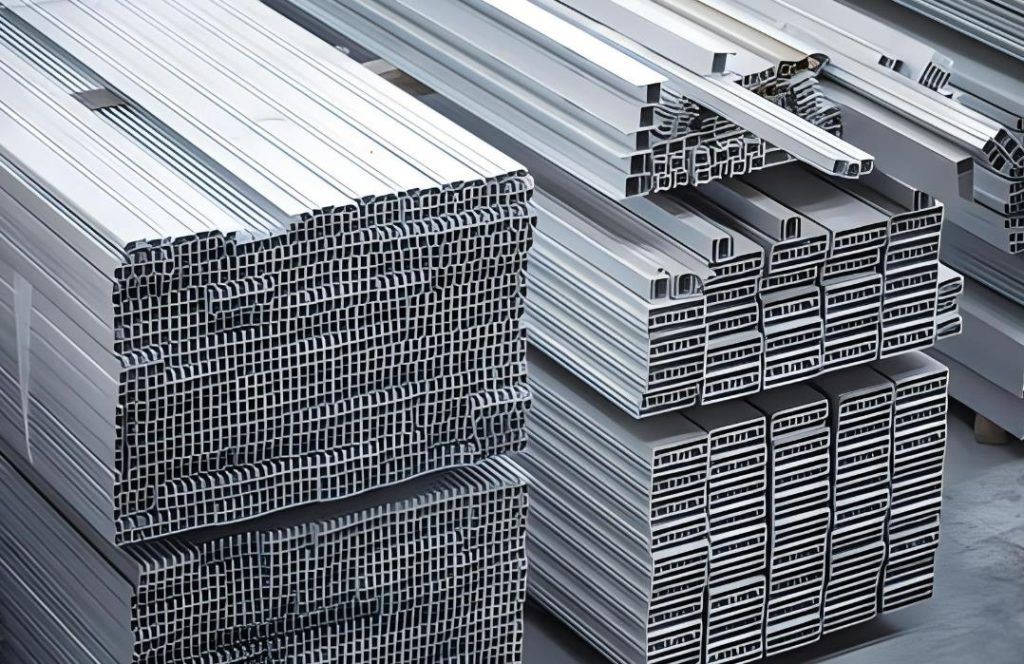