Aluminum stands as a cornerstone material across a myriad of industries, lauded for its exceptional ductility, low density, superior electrical and heat conductivity, corrosion resistance, and sleek appearance. This versatile metal finds its purpose in a vast array of applications, from delicate instruments and electronics to robust machinery and automation systems. Central to its industrial use are aluminum casings, which protect and house various components. But when it comes to aluminum casings, two primary forms stand out: die-cast and extruded aluminum. Each type has its unique manufacturing process, characteristics, and applications.
The Basics of Aluminum Casings
Aluminum alloys are favored for casings due to their optimal combination of strength, weight, and conductivity. These properties make aluminum casings indispensable in sectors such as electronics, communication, automation, and even in the manufacturing of smart cards and sensors. The question then arises: when is it preferable to use die-cast aluminum casings, and when are extruded aluminum casings more suitable?
Extruded Aluminum
The extrusion process involves pressing aluminum rods through a die, under high pressure, to create profiles that are essentially extended two-dimensional shapes. This method allows for the production of long, continuous sections, typically up to 6 meters due to equipment limitations. Extruded aluminum is renowned for its uniformity and strength, making it ideal for structural components. However, its shapes are limited to those that can be achieved through this linear pressing process.
Die-Cast Aluminum
In contrast, die-casting offers a leap in complexity and versatility. By melting aluminum alloy and injecting it into a three-dimensional mold, manufacturers can achieve intricate shapes and designs not possible with extrusion. This process allows for the creation of components with complex geometries, including hollow spaces and non-linear forms. The die-cast aluminum casing is particularly valued for its aesthetic flexibility and the ability to meet stringent design requirements.
Choosing Between Die-Cast and Extruded Aluminum
The choice between die-cast and extruded aluminum hinges on several factors. Die-cast aluminum is the go-to for applications requiring complex shapes, detailed designs, or enhanced aesthetic appeal. Its ability to form watertight seals also makes it indispensable in applications where waterproofing is crucial. However, the higher costs associated with die-casting — from mold production to processing — make extruded aluminum a more cost-effective option for straightforward, linear profiles.
Despite the versatility of die-cast aluminum, extruded aluminum remains more prevalent due to its efficiency and lower production costs. It serves as a testament to the principle of selecting the right material and process based on the specific needs of the application, rather than a one-size-fits-all approach.
Conclusion
Understanding the distinctions between die-cast and extruded aluminum casings is essential for professionals in industries reliant on these materials. By recognizing the unique benefits and limitations of each type, manufacturers and designers can make informed decisions, ensuring the optimal use of aluminum in their projects. As aluminum continues to play a pivotal role in technological and industrial advancements, the knowledge of its applications and processing methods becomes increasingly valuable.
This exploration into the realms of die-cast and extruded aluminum not only sheds light on their differences but also highlights the importance of material selection in achieving innovation, efficiency, and effectiveness in product design and manufacturing.
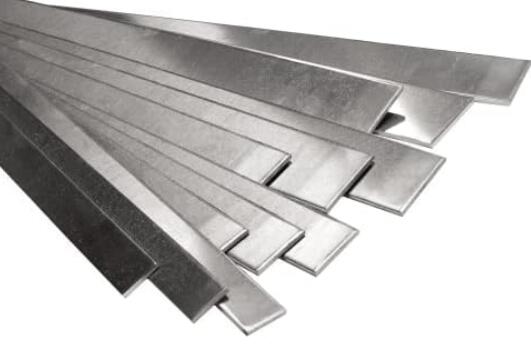