Introduction
Aluminum plates play a crucial role in modern industrial applications, offering a range of properties suited to diverse needs. Among the various types available, 5052 and 6061 aluminum plates stand out due to their distinct characteristics and applications.
Different Performance Characteristics
When considering aluminum plates, understanding their performance distinctions is essential:
5052 Aluminum Plates: Known for their fatigue resistance, corrosion resistance, and excellent weldability. They are highly malleable and can be polished for aesthetic applications. However, they cannot undergo heat treatment, have limited plasticity during cold hardening, and may pose challenges in machining.
6061 Aluminum Plates: Renowned for their corrosion resistance, weldability, and superior oxidation effect. They contain magnesium and silicon, offering robust structural integrity and versatility across various industrial sectors.
Scope of Application
Each type of aluminum plate serves specific purposes:
5052 Aluminum Plates: Ideal for environments requiring rust-proof properties, commonly used in marine and architectural applications.
6061 Aluminum Plates: Preferred in industries demanding high strength and durability, such as aerospace and automotive manufacturing.
Alloy Elements
The composition of alloy elements distinguishes these plates:
5052 Aluminum: Primarily composed of magnesium.
6061 Aluminum: Contains magnesium and silicon, enhancing its mechanical properties and corrosion resistance.
Different States and Uses
Understanding their states and applications aids in selecting the right aluminum plate:
5052 Aluminum: Available in states like H112, H24, and H32, suitable for bending and forming.
6061 Aluminum: Offered in states such as T6 and T651, known for their hardness and utility in structural components and molds.
Conclusion
In conclusion, the choice between 5052 and 6061 aluminum plates hinges on specific project requirements. Whether prioritizing corrosion resistance, formability, or mechanical strength, each type offers unique advantages tailored to diverse industrial applications. By understanding these differences, manufacturers and engineers can optimize material selection to achieve optimal performance and durability.
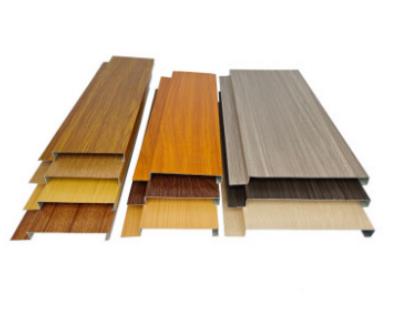