Introduction
In the realm of aluminum applications, surface treatment stands as a pivotal aspect, ensuring not only enhanced durability but also aesthetic appeal. Among the various techniques, hard anodizing emerges as a frontrunner, boasting the ability to augment corrosion resistance, hardness, and surface quality. Delving deeper, let’s explore the fascinating world of hard anodizing and its color variations, unveiling a spectrum of possibilities for industries reliant on aluminum.
Basic Principles of Hard Anodizing
Hard anodizing operates on a fundamental principle – the creation of a dense oxide layer on aluminum alloy surfaces. This layer, imbued with exceptional hardness and corrosion resistance, serves as a shield, safeguarding the material against environmental adversities. Its significance reverberates across diverse industries, finding applications in aerospace, automotive, construction, and electronics.
Applications of Hard Anodizing
The aerospace sector relies heavily on hard anodizing for critical components, ensuring longevity amidst demanding conditions. Similarly, in the automotive domain, hard anodized parts endure rigorous usage, exemplifying resilience and reliability. Even in the construction realm, hard anodizing finds its niche, elevating aluminum’s suitability for architectural purposes. Moreover, the electronics industry benefits from the protective prowess of hard anodizing, safeguarding delicate gadgets from wear and tear.
Color Variations in Hard Anodizing
One of the most intriguing aspects of hard anodizing is its ability to don various hues, offering a spectrum of options for designers and engineers. From classic blacks and grays to nuanced browns and opulent golds, the palette is as diverse as it is captivating. Controlling factors such as temperature and voltage during the oxidation process play a pivotal role in achieving desired colors, with special chemical solutions unlocking unique possibilities.
Enhancing Aesthetics Through Hard Anodizing
Beyond functionality, hard anodizing serves as a canvas for aesthetic expression. Dyeing and sealing processes further augment the visual appeal, allowing for customization and personalization. Surface finishing techniques add a layer of gloss, elevating the allure of aluminum components in various applications. In an increasingly design-conscious world, the aesthetic dimension of hard anodizing holds immense significance, resonating with discerning consumers and industry professionals alike.
Conclusion
In conclusion, hard anodizing emerges not only as a cornerstone of surface treatment in aluminum applications but also as a testament to human ingenuity and innovation. Its ability to fortify, beautify, and customize underscores its indispensability across a spectrum of industries. As we navigate towards a future marked by technological advancement and aesthetic refinement, hard anodizing stands poised to play an ever-expanding role, shaping the world of aluminum applications in profound ways.
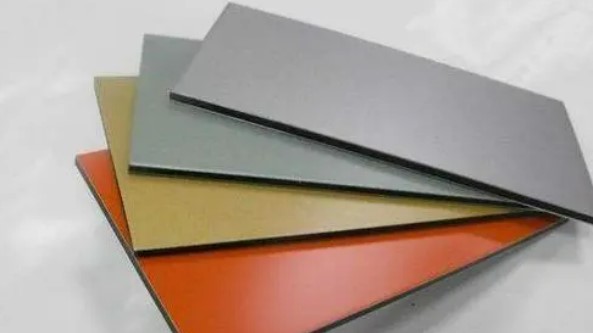