Introduction
In the realm of aluminum processing, the oxide film on an aluminum alloy roll serves not just as an aesthetic enhancer but also as a protective layer against external damage. However, a common issue faced in aluminum oxidation is uneven coloring. Understanding the causes of this irregularity is crucial for professionals in the field.
Excessive Working Area Size
A primary factor contributing to uneven coloring is the size of the working area. When too large, it can lead to inconsistencies in the oxidation process. The variance in the swing within the solution results in different exposure levels across the surface, causing an uneven color distribution in the oxide film. Managing the working area size is vital for maintaining color consistency.
Material Composition Issues
The composition of the aluminum alloy coil plays a significant role in the oxidation outcome. When the outer layer comprises high-quality aluminum alloy and the inner layer contains mixed aluminum, the disparity can lead to uneven coloring post-oxidation. This issue is often manifested as vitiligo-like spots, particularly evident when different qualities of aluminum are combined.
Process Operation Challenges
Another challenge arises from the operational aspects of the process. Incomplete alkaline etching treatment can leave behind parts of the original oxide film and dirt, affecting the uniformity of the color. Additionally, performing alkaline etching immediately after light treatment without neutralizing the surface’s alkalinity can lead to color irregularities. Ensuring the workpiece does not come into contact with foreign substances during transfer is also crucial for preventing uneven coloring.
Strategies for Prevention and Quality Control
To mitigate these issues, professionals must carefully manage the working area size and ensure the consistency of the aluminum material used. A thorough and well-managed alkaline etching process, along with careful handling to avoid contamination, is essential for achieving a uniform oxide layer.
Conclusion
The challenges of uneven coloring in aluminum oxidation can be addressed through meticulous attention to the size of the working area, material composition, and process operations. Understanding and addressing these key factors are essential for professionals dedicated to achieving the highest quality in aluminum finishing. This knowledge not only enhances the aesthetic appeal but also ensures the longevity and durability of the aluminum products.
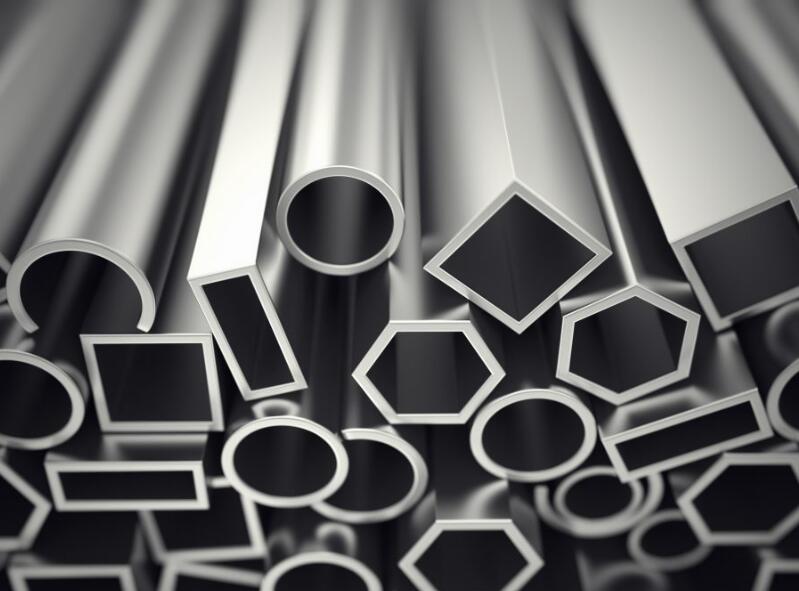