Introduction
Aluminum alloys are pivotal in various sectors, from aerospace to automotive, owing to their exceptional blend of strength, lightness, and resistance to corrosion. One critical factor that enhances these properties to meet specific application requirements is heat treatment. This guide delves into the prevalent heat treatments for aluminum alloys, shedding light on their processes, impacts, and applications.
Annealing Process
Annealing is a heat treatment process that mitigates the effects of cold working, a method of strengthening aluminum alloys without heat. Cold working increases internal stresses, strength, and hardness but at the expense of ductility and formability. Annealing resets the crystalline structure, relieving internal stresses and enhancing formability, enabling further shaping with lower forces and greater deformation tolerance. The process involves precise heating, maintaining specific temperatures, and gradual cooling, ensuring cast aluminum parts are stress-free and less prone to future cracking.
Solution Heat Treatment
Solution heat treatment, akin to annealing, involves heating the alloy but differs in the cooling phase, where quenching “freezes” the microstructure. This process enables hardening through aging, while also providing a window for additional forming processes. It maximizes the concentration of hardening alloying elements in the solid solution, requiring precise temperature control to achieve optimal solubility just below the alloy’s melting point.
Aging: Natural and Artificial
Aging follows solution heat treatment, enhancing the strength and hardness of the alloy. Natural aging rapidly increases hardness within the first 24 hours, reaching full effectiveness in four to five days. However, some alloys require artificial aging, or precipitation hardening, involving further heating to achieve complete precipitation, thereby increasing strength and hardness at the expense of ductility.
Homogenizing Heat Treatment
Homogenizing aims to redistribute internal alloying elements for a homogeneous product chemistry, crucial for castings that solidify at different rates. Conducted at higher temperatures than annealing, it ensures even chemistry throughout the product, preventing inconsistencies in hardness and brittleness, and ultimately enhancing product durability and performance.
Applications and Impacts
Heat-treated aluminum alloys find applications across diverse fields, from aircraft components to automotive parts. Understanding and selecting the appropriate heat treatment process is vital for optimizing product performance, durability, and application suitability.
Conclusion
The intricate world of aluminum alloy heat treatments is pivotal for enhancing material properties, ensuring products meet stringent performance and durability requirements. Whether through annealing, solution heat treatment, aging, or homogenizing, each process plays a crucial role in unlocking the full potential of aluminum alloys.
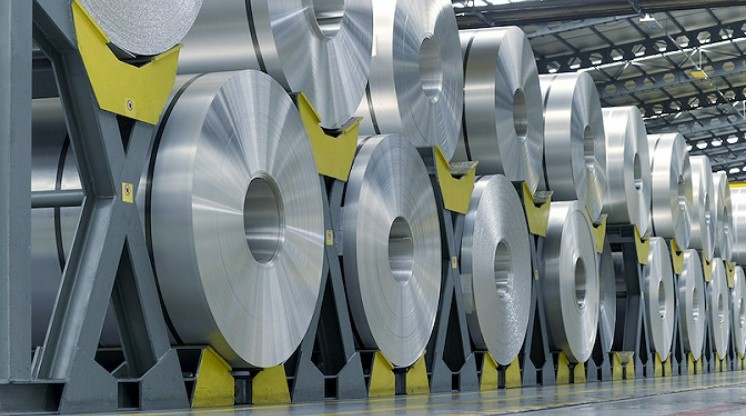