Introduction
Aluminum profiles play a pivotal role in modern architecture, manufacturing, and engineering, serving as the backbone for various structures and products. Their production is a meticulous process, requiring specialized extrusion equipment and precise temperature control. This article explores the intricate process behind aluminum profile production, highlighting the technology and precision that make it possible.
Section 1: Overview of the Aluminum Profile Production Line
The production of aluminum profiles necessitates a comprehensive line of six essential pieces of equipment: the extrusion machine, long rod hot shearing furnace, alloy aging furnace, mold furnace, tractor, and cooling bed. Each plays a critical role in transforming raw aluminum into finely crafted profiles. From heating and molding to cooling and aging, every step is vital to achieving the desired quality and specifications.
Section 2: The Production Process Step-by-Step
- Material Preparation: The journey begins with aluminum rods being carefully laid on the material rack of the hot shearing furnace, ensuring they are flat and unstacked to prevent accidents and mechanical failures.
- Heating the Aluminum Rods: Rods are heated to about 480°C, undergoing a precise warming process crucial for their malleability in extrusion.
- Mold Heating: Simultaneously, molds are heated to match the aluminum rods’ temperature, preparing them for the extrusion phase.
- Extrusion Process: Once heated, the mold is placed into the extruder’s die base, and the aluminum rods are sheared and fed into the extruder to be shaped into profiles.
- Cooling and Cutting: After extrusion, profiles pass through a cooling stage before being cut to fixed lengths, a step that demands precision for uniformity.
- Finishing Touches: Profiles are then transferred for modulation and correction, ensuring they meet stringent quality standards before undergoing aging to achieve ideal hardness and size.
Section 3: Quality Control and Finishing
Quality control is interwoven throughout the aluminum profile production process. Each step, from extrusion to aging, is monitored to ensure the profiles meet exacting standards. The final inspections are just as crucial, ensuring each profile is ready for the market and can withstand the demands of its intended application.
Section 4: Applications of Aluminum Profiles
The versatility of aluminum profiles is evident in their widespread use across construction, automotive, and aerospace industries, among others. Their strength, lightweight nature, and corrosion resistance make them invaluable in framing, structural components, and countless other applications.
Conclusion
The production of aluminum profiles is a testament to the advancements in modern manufacturing, blending precision engineering with specialized equipment to create materials that shape our world. As we’ve seen, each step in the production process is critical to ensuring the final product’s quality and reliability, highlighting aluminum’s continued significance in pushing the boundaries of innovation across various sectors.
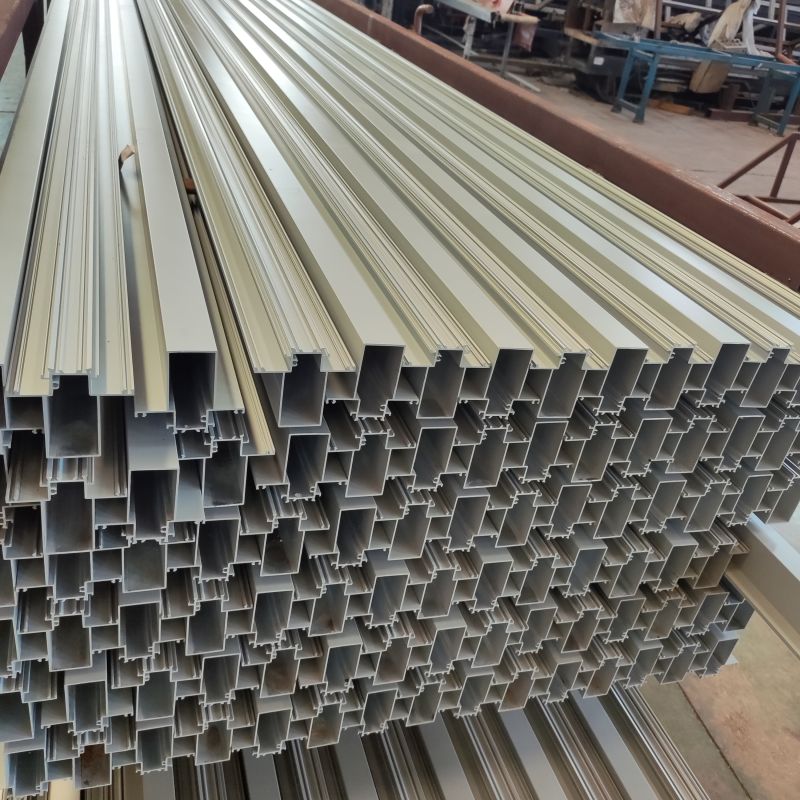