Introduction
Have you ever wondered why your meticulously welded aluminum alloy exhibits unsightly black lines after undergoing anodizing? This phenomenon often perplexes engineers and manufacturers alike. In this comprehensive guide, we delve into the intricate world of aluminum metallurgy to uncover the underlying reasons behind black line formation and explore effective strategies for their removal.
Understanding the Root Causes
When aluminum alloys undergo welding, high temperatures induce metallurgical changes, leading to the formation of thick oxide films at specific positions. The relationship between phase structure and color further elucidates how elements like Si, Mg, Fe, Cu, and Mn influence intermetallic compounds, ultimately contributing to the appearance of black lines on the surface.
Effects of Black Lines
Beyond mere aesthetics, black lines can adversely affect the functionality and integrity of aluminum alloy products. Understanding the contexts in which black lines commonly manifest is crucial for devising targeted solutions.
Detailed Analysis of Probable Causes
Examining the intricate nuances of pretreatment alkaline etching pools, chemical polishing scale imbalances, and oxidation tank parameters provides valuable insights into the root causes of black line formation.
Solutions to Remove Black Lines
Implementing clean production practices, conducting regular analyses of impurity content in tank liquids, employing effective degreasing techniques, and optimizing parts processing procedures are key strategies for mitigating and eliminating black lines from welded aluminum alloys.
Conclusion
In conclusion, the presence of black lines on welded aluminum alloys is a multifaceted issue with significant implications for product quality and performance. By understanding the underlying causes and implementing targeted solutions, manufacturers can ensure the production of flawless aluminum alloy products that meet the highest standards of excellence.
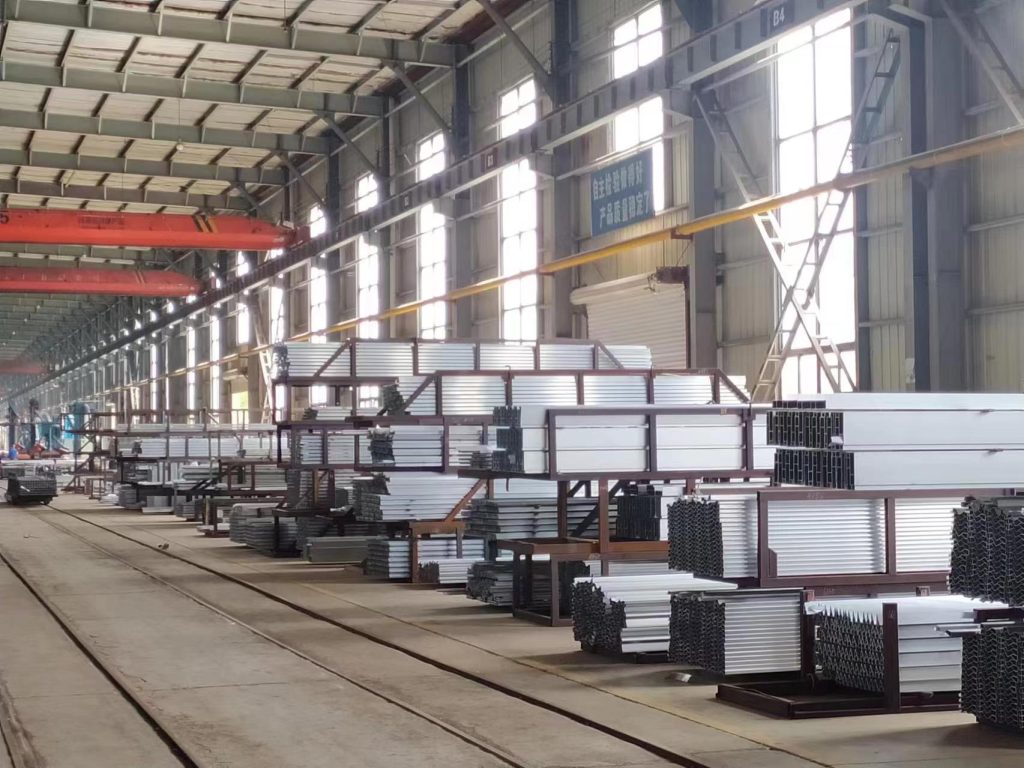