Introduction
In the realm of aluminum profile processing, electrophoretic coating stands as a game-changer, offering a myriad of benefits that elevate both functionality and aesthetics. This article delves into the transformative advantages of electrophoretic coating, shedding light on its role in shaping the future of aluminum profiles.
Advantages of Electrophoretic Coating
Control over Coating Thickness: Electrophoretic coating provides unparalleled control over the thickness of the coating film, ensuring precision and consistency in application.
Strict Process Requirements: Rigorous process standards contribute to improved yield and quality of industrial aluminum profiles, enhancing overall efficiency.
High-Quality Coating Film: The resulting coating film boasts exceptional decorative effects and corrosion resistance, thanks to the utilization of acrylic resin solidified with amino resin.
High Application Efficiency: With low paint viscosity and efficient recycling equipment, electrophoretic coating achieves over 95% application efficiency, minimizing wastage.
Automation-Friendly: The process lends itself seamlessly to automated production, facilitating streamlined assembly line operations and maximizing productivity.
Time and Manpower Savings: Compared to traditional processes, electrophoretic coating saves time and reduces labor costs, eliminating the need for pore sealing and associated complications.
Even and Dense Coating: The technique ensures uniform coating even on complex aluminum profiles, offering superior protection and finish.
Additional Benefits of Electrophoretic Coating
Beyond the outlined advantages, electrophoretic coating enhances the safety and light transmission performance of aluminum profiles, broadening their scope of applications across various industries.
Conclusion
Electrophoretic coating emerges as a cornerstone of innovation in aluminum profile processing, unlocking unprecedented levels of control, efficiency, and quality. As industries continue to evolve, the adoption of this advanced technique promises to revolutionize the aluminum landscape, paving the way for a brighter and more sustainable future.
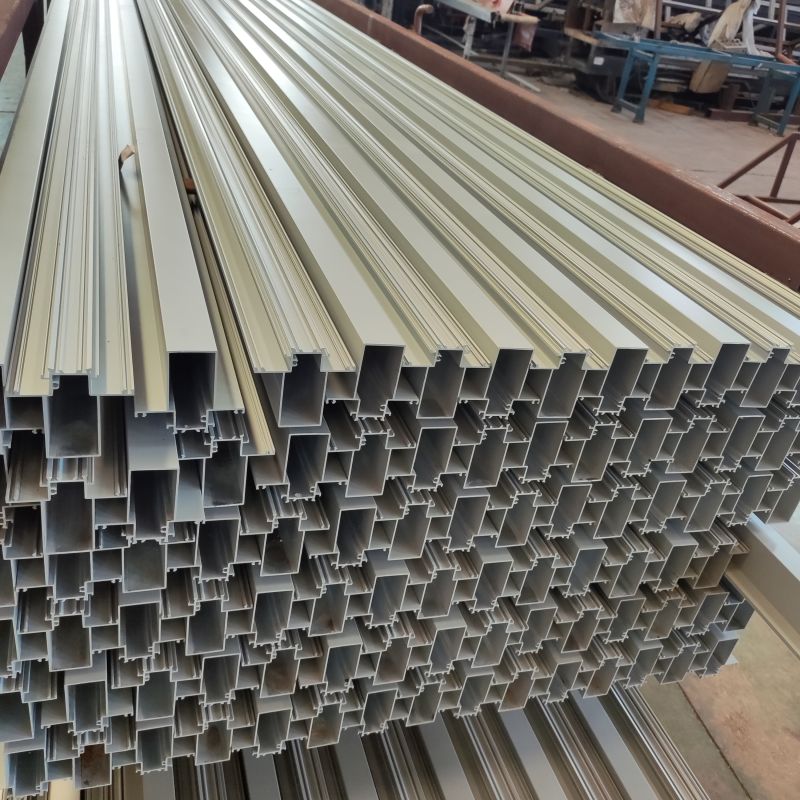