Rina takes you on today’s journey together
Hey there, aluminum aficionados! Rina Meng here, ready to unravel the mystery behind why industrial aluminum profiles are often referred to as assembly line aluminum profiles. Get ready for a wild ride as we dive deep into the world of aluminum and its connection to those magnificent assembly lines!
Now, let’s start with a little background. We all know that assembly lines are the backbone of industrial production. They’re like the superheroes of manufacturing, saving costs and streamlining the production process. Picture those mesmerizing conveyor belts, the synchronized movements, and the symphony of machinery. It’s a sight to behold!
So, why do we call them assembly line aluminum profiles? Well, my friend, it’s all about their role in the construction of assembly line equipment. These aluminum profiles are like the unsung heroes, providing the sturdy framework that supports the entire operation. They’re the backbone of the assembly line, the hidden champions behind the scenes.
Imagine an industrial aluminum profile workbench, standing tall and proud, ready to assist workers in their daily tasks. Or think about the double-speed chains and support racks that keep the assembly line conveyor lines running smoothly. These profiles are the unsung heroes, the silent supporters of the assembly line revolution.
But hey, let’s dive into the nitty-gritty of why these profiles are so crucial in the assembly line realm. There are a few factors at play here, my friend.
Firstly, it all starts with the quality of the casting rod. You see, the surface and extrusion forming of aluminum profiles for heat dissipation fins can be influenced by the quality of the casting rod. We’re talking about factors like slag inclusion, looseness, coarse grain size, segregation, and bright grain size. These defects can affect the welding and flow of the aluminum, resulting in what we call “adsorbed particles.” It’s like a party crasher that hitches a ride on the aluminum profile, causing a disruption in the smooth flow of production.
Next up, we have the influence of the die. During the extrusion process, the die undergoes high temperature and pressure, leading to elastic deformation. The working strip of the mold transforms into a trumpet-shaped shape, with only the blade part coming into contact with the adhesive aluminum. This interaction can lead to the formation of those pesky “adsorbed particles.” It’s like a tool chip lump that just won’t let go!
Last but not least, the extrusion process itself plays a role in this aluminum bonding adventure. The selection of extrusion process parameters is crucial. If the temperature is too high or the speed is too fast, those “adsorbed particles” can multiply like rabbits at a carrot farm. The flow speed increases, the mold deformation intensifies, and the metal’s resistance to deformation weakens. It’s a recipe for aluminum adhesion gone wild!
But fear not, my aluminum-loving friends! We can overcome these challenges. By analyzing problems, gaining experience, and fine-tuning our production practices, we can reduce or even avoid these “adsorbed particles” altogether. It’s all about continuous improvement and striving for excellence in our aluminum profiles for heat dissipation fins.
Overall, industrial aluminum profiles are rightly called assembly line aluminum profiles because of their vital role in the construction of assembly line equipment. They are the unsung heroes, providing the framework that supports the entire operation. So, the next time you see an assembly line in action, take a moment to appreciate the aluminum profiles that make it all possible.
And with that, my dear readers, I bid you farewell. Thank you for joining me on this aluminum adventure! Remember, when life gives you aluminum, build a sturdy framework and let the assembly line magic unfold. Until next time, stay aluminum-some!
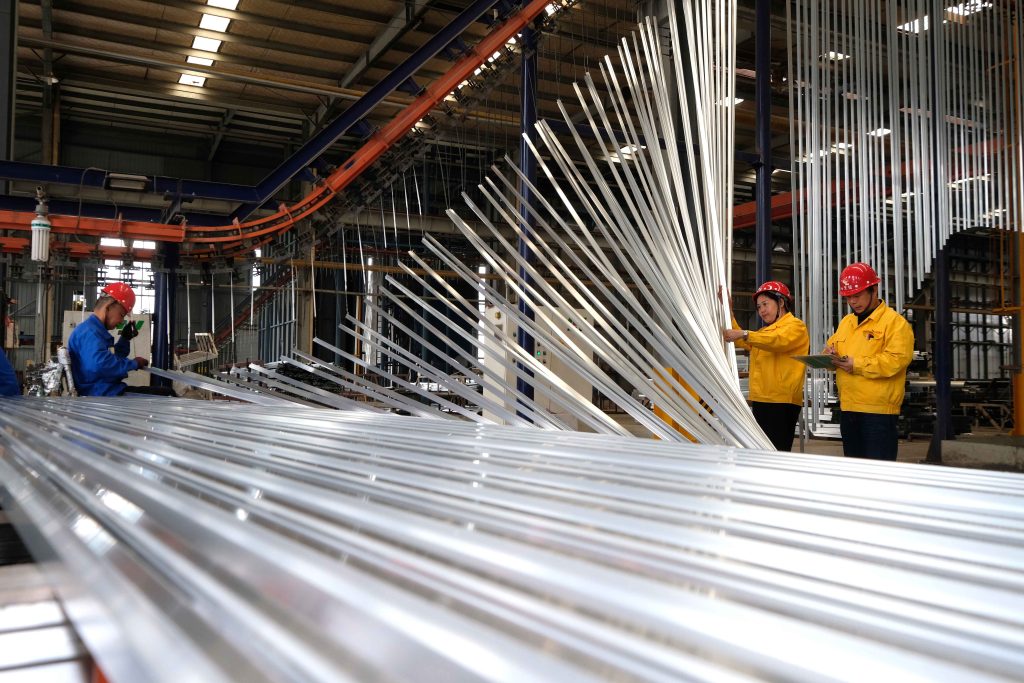